A can of worms
Multiple factors contribute to ‘leaky buildings’ (those built in the 1990s and early 2000s, although others do leak). Frequently cited causes include design, installation and/or choice of materials, the use of methods unsuitable for New Zealand weather, poor workmanship … the list is long.
So, with a focus on the physical aspects in this article, a wet, windy day in Wellington seems fitting for a site visit to the remediation of five leaky townhouses in Brooklyn. After six months Holmes Wellington has nearly completed the project, working around the residents as they strip out decayed materials and do repairs to current code. The last skip full of wasted insulation and rotten timber waits to go to landfill.
The Wellington townhouses are apparently typical of the unpredictable and complicated nature of the leaky building problem. Visible symptoms were no indication of the extent of the damage or the cost of repairs says Colette Mullin of Melling Architects who redesigned the repairs for south, west and east facades.
The property was built using the classic non-traditional construction methodology of the early 1990s with monolithic cladding, fiberglass insulation and plasterboard lining. The north façade with balconies had shown signs of failure several years ahead of the rest of the building and had been replaced by the body corporate.
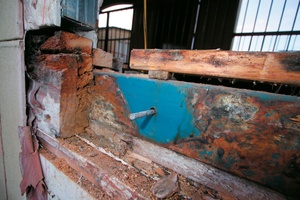
Interior mold in a ground floor apartment indicates the flow on effects of leaking windows, which had been installed throughout without flashings, and sealed with silicone. The cladding failed on the corners, and, as there were no wall cavities to allow water egress, the treated timber framing behind rotted.
“The cladding was fixed directly to the stud with occasional cracking on the joints and water seeps in straight against the stud,” says Holmes Wellington project manager Brent Pitkethley. “The cladding seems to act like blotting paper and effectively stays soaked the whole time.”
Lack of adequate ground clearance in the south-west corner allowed water up into the building while water ran down the south façade from the pitched, gutter less, monolithic clad roofs on the projecting bays. “The treated timber framing at the ground floor under the inclined monolithic roof was completely rotten. You could put your finger through it,” Mullin says. They discovered this when they opened up the building. Concrete tiles and guttering have since replaced the original, unsuitable roof cladding to these bays and larger windows installed with flashings, which Mullin detailed in the drawings.
On advice from a timber remediation specialist structural timbers were replaced in the entire ground floor of the south façade and two-thirds in the two upper storeys. On the east and west they replaced about half. Three steel lintels were also re-treated. The structure had to be propped to do the work, which added to the cost. Exterior weatherboard cladding, proven in Wellington conditions replaced the failed material and is fixed to a cavity, which gives a ventilated drainage cavity. Mullin says they went for a “belt and braces” weatherproofing solution as the building is in a very high wind area.
The final cost will exceed the provisional sum in the contract, and the client’s contingency sum Mullin says, as, typical of these projects, it was impossible to accurately estimate the full extent of the repairs. Like other remediation specialists, Thomas Wutzler, a consultant with Helfen, a building surveying company, is very familiar with the insidious and costly nature of leaky buildings.
As well as project managing new builds he investigates and advises on leaky building repairs, working over the past 10 years for a variety of clients through dispute processes.
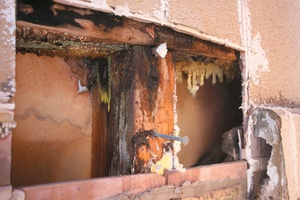
Much of the remedial work the company does requires the replacement of inherently flawed building facades, correcting structural, acoustic, insulation and fire rating deficiencies and internal moisture problems. He says a growing percentage of his clients require remediation of failed repairs. He was disappointed to see the ‘reclads to reclads’ in Vancouver in 2004, then several years later the same mistakes being made in New Zealand. “The extent of repairs can only be decided upon after gaining a full understanding of the building and its façade as well as the wind pressures and other forces to which the building is likely to be subject,” Wutzler says.
Numerous failures are the result of inadequately thought through details and poorly constructed complex features. Many clients opt to simplify the design, save on construction cost and time and improve the overall look. When asked to check a seemingly innocuous problem such as a leaky window Wutzler says experience quickly tells him if it is part of a larger systemic problem which has to be confirmed by further destructive investigations such as drilling holes, measuring moisture contents and water testing.
They talk to the owners immediately about the options, but for many, repairing the building won’t be feasible and the investigations stop there. Risks include water ingress, degradation of building materials, growth of fungi and subsequent health issues. In cases where stachybotrys chartarum is growing these can be serious. Long-term respiratory illness can result from living in damp conditions.
Called in to investigate a few minor concerns in relation to water ingress at a 47-unit apartment complex Wutzler found multiple failures and poor workmanship, which required several million dollars’ worth of redesign and repairs. The balconies and upper level walkways were so decayed that several fell down when temporary props installed as a safety precaution were removed. Opening up the walls revealed many steel portals through the building weren’t fixed to the foundations. “When you start taking off the cladding you frequently find more defects and damage and not just weather-tightness defects – structural issues, fire issues as well as internal moisture problems such as water condensing under the roof.”
He says it’s important for a remediation specialist to be present when cladding is removed to assess and understand the causes of water ingress, and to be confident that any remedial plan will address the issues. It is also important to assess the condition of the timbers.
“A lot of people will look at the building, particularly if the cladding has been off and it’s dried out, and say - there’s not too much wrong there.” At certain stages of decay timber can look sound to untrained eyes but the structural integrity has gone. Extensive, in-depth repairs to the 47-apartment building simplified the design, making it more functional, lighter inside and weather tight.
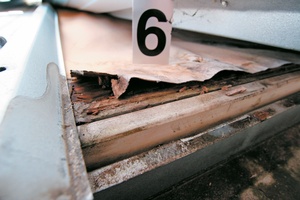
There is no simple resolution to leaky building problems. Wutzler suggests improvements such as further education through all sectors of the building industry with a focus on building science, better co-ordination between the various parties and better use of time and materials. Many leaky buildings remain to be repaired or replaced.
A 2009 Pricewaterhouse Coopers report estimated that 42,000 dwellings were likely to be leaky homes, costing around $11.3 billion (2008 dollars). Philip O’Sullivan, director, Prendos building surveyors, allows a similar amount for commercial and other buildings. “All up my best guess … is $14 - 15 billion with this figure increasing as building costs escalate.”
O’Sullivan thinks with the “current level of denial” among home owners coupled with [in] ability to pay for repairs there is likely to be 30 years worth of work to repair 80 per cent of leaky buildings, with around half the national quota located in Auckland. “People are living in comfort in mid to high-income dwellings with no evidence of the problem as yet and the average person has no way of knowing,” O’Sullivan says.
He speculates that a significant number of residential complexes have been repaired, as well as schools, whereas “we have only dealt with the tip of the stand-alone residential dwellings and I suspect the same applies to affected commercial and other buildings.”