A street in the sky
Construction started on this flagship 10-storey building in May 2013 - the first residential high rise in West Auckland to be approved under the new Unitary Plan requirements. Built on top of the part footprint of an existing four-level carpark, the tower presented a set of unique challenges, with construction starting 16 metres above the ground.
The tower is stage one of a two-stage project that will see a residential street built on top of the remainder of the carpark roof, in which 16 duplex houses and four single-storey units will complete the development.
Kalmar project manager Nathan Halloran said the initial carpark, which was completed early last year, is situated in the centre of New Lynn township. It was future-proofed with the knowledge that the 10-storey tower would eventually be built over part of its footprint.
“The strengthening works were built into the design and undertaken during the base-build period. Included in the base-build strengthening was allowance for the tower crane load reactions,” Mr Halloran said. When construction of the tower started, some work was required to modify aspects of the carpark to ensure the construction programme had no effect on day-to-day operation of the carpark, or existing building services.
“The initial establishment on site required some novel protection schemes across the existing stairwell and lift shaft. In order to protect the carpark patrons a series of temporary crash decks were installed after hours, which meant the lift was able to continue operating without interruption.”
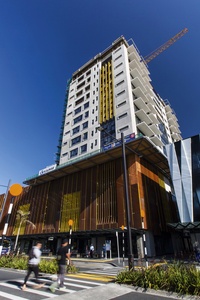
One of the carpark’s stairwell/lift overruns required demolition in order for the tower’s structural transfer slab to be constructed. This meant one lift shaft was pulled apart, lowered an entire floor, and then a 16mm steel protection plate was put on top of the lift so its operation could be maintained.
Mr Halloran said the demolition and reconfiguring of the stairwell/lift overrun placed added pressure on the construction schedule as a significant amount of time was lost while this phase was completed. “However, working together with engineers Buller George Turkington (BGT), we came up with a way to make up the lost time by leap-frogging the structure. The central core was completed utilising a jump-form concrete formwork system,” he said.
“The steel structure was designed with joint splices on every second level, which meant with careful coordination, we were able to pour the upper level first enabling the structure to continue progressing up while workers went back to complete the lower floor structure. It enabled us to maintain a cycle as the structure went up and we were actually able to collect time as the structure got higher.”
This unique methodology meant two floors were built every 10 days, and by the time the team got to the upper floors, that cycle had reduced to eight days per two floors. Each floor will house ten one- and two-bedroom apartments ranging between 45 and 65m2.
Significant planning was required not only to maintain access for the public in the operating spaces below, but also to maintain access for deliveries and lifting materials. “When demolition of the overrun was completed we put a catch screen up on that level (level four). We also employed additional gate people to control the public walking around the project so when we were lifting materials above footpaths, there were staff on the ground ensuring the public was safe,” Mr Halloran said.
“But New Lynn sits in a depression so the site is in a bit of a wind tunnel. This meant a lot of the time we weren’t able to lift what we needed when we wanted to. So for the month of January we worked through the night, just lifting. Because the central core was built with the jump form system it allowed us to build the lift shaft five floors above the rest of the structure, but it meant we were dealing with extremely challenging windy conditions.”
In order to lift materials to the upper floors after the roof was completed, the team came up with a variety of ways to allow this, including crane platforms on the side of the building. The 80-tonne tower crane was literally suspended above a ramp on level four leading down into the carpark. “It was hung off four building columns. The vertical load went into the ground but the shear load was taken up with eight bolts. It was not attached to the building at all,” Mr Halloran said.
The unique building design allowed the client significant flexibility with apartment layouts. No structural shear walls run through the building, which meant wide-open floor plates were possible. “Following the Canterbury earthquakes more emphasis has been put on physical separations between opposing structures,” Mr Halloran said. “It is what’s not in this structure that is interesting. BGT designed a 75mm clear opening on all four building corners allowing the pre-cast cladding panels to move in a seismic event without impacting each other, and preventing debris falling from the building. The joints are exposed and left open, which is virtually unheard of in this type of construction.”
The tower will be serviced by two passenger lifts. Exclusive residents’ parking will be housed on the top floor of the existing carpark, however the building’s location is extremely unique in Auckland in that it is situated directly adjacent to a major transport hub.
Final design for stage two of the development is currently underway.