All in the family
For some in the building industry, the image of the architect is one who sketches out a building, then sends it out into the world to be realised, without much thought for how this might happen. Dave Strachan is turning this idea on its head with his own team at Strachan Group Architects (SGA), via the creation of his new offices, which combine architecture office with workshop, landscaping and fabrication businesses – all in one cohesive home.
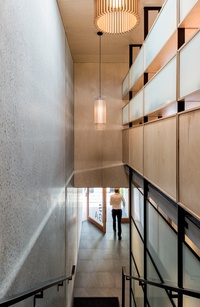
For Strachan, the realisation of this building is something of a dream come true. He and his wife bought the plot of the land it stands on some years before, with the hope of creating an office to house his growing architecture firm, and also the work of his three sons, who are all in the building industry.
One son owns Strachan Group Landscape Architecture (SGLA), which lives beneath the architecture offices, and the other two sons’ fabrication business, Crate Innovation, is contained in a double-storey space adjacent, which shares a concrete wall with the other two businesses.
The workshop, located to the rear of SGLA’s office, is key to the way in which SGA works, as all staff are encouraged to build, tinker and create downstairs. “It’s amazing how much the staff use the workshop, anything from repairing chairs to personal items,” says Strachan.
“You learn by doing stuff. Instead of just drawing on the computer, you actually make the connection to how things work. We’re mates with the building contractors because we work together, instead of butting heads over projects. We’re on the same side.”
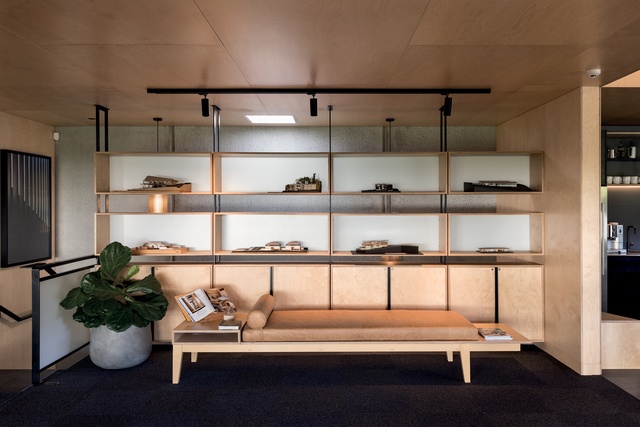
The creation of the building was also a family affair – if you can stretch the term to include the architecture team. Crate Innovation did all the building, while the architects created all the cabinetry inside, which is made from plywood – the same as the walls and parts of the ceiling – and is designed to blur the boundaries between furniture and construction. Aside from where the design called for a folded metal junction, almost everything in the studios has been made by the people who use it.
The style of the offices is also family-friendly, says Strachan. “You spend loads of time with the people you work with, so we have tried to make it a family environment, with a lounge-style café area, where you will commonly see people cooking.”
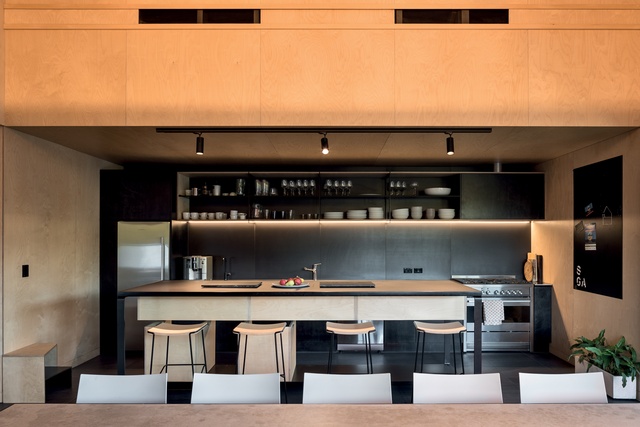
The lounge area has sliding doors that convert the corner of the space into a kind of internal verandah. “This is something we try to do with our projects, so you can feel like you’ve been outside without actually leaving the building,” says Strachan. “We have a residential interface here, so it is good to engage with the street. We want to be a good neighbour.”
Externally, the building has a residential look, with concrete and painted plywood cladding that has a Trespa high-pressure laminate rainscreen laid over. The most engaging aspect of the exterior is the windows, which are expressed and can each be opened individually to different heights, creating an activated façade. These same windows are also engaging inside, where they operate through a cog-like, custom-made winder.
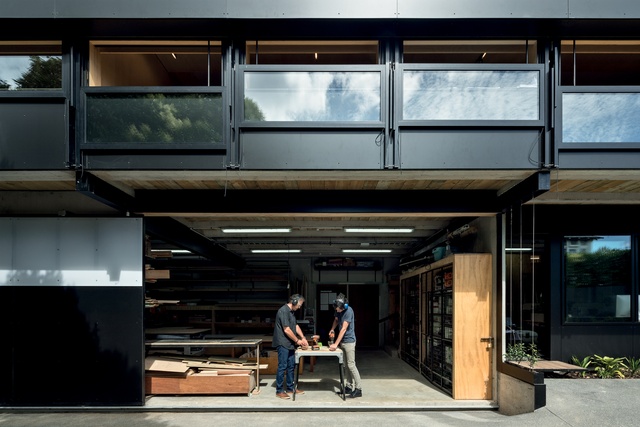
“Our oldest son and one of my students decided we needed a chain of some sort to make the windows operable, and they made a primitive bike chain to drive it up and down, as a sample,” says Strachan. “We said yeah, well done guys, because that’s where it’s nice being proactive between builders and architects. We’ve taken that idea and we’ve done it with a rack and pinion, and it just goes up and down on the winder.”
While the building does not have a Green Star certification (“too niggly,” says Strachan), it has many eco-friendly and passive design features. The workspaces are lit with solar tubes. A solar fan sucks air through the building, creating passive air conditioning. Both ends of the office can be opened up with sliding doors, allowing a breeze through.
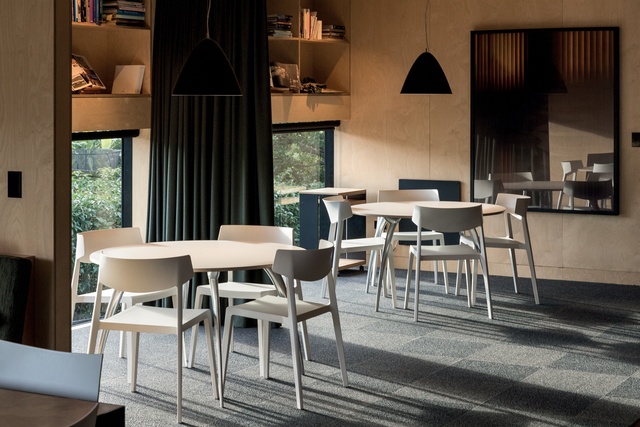
The only heating is via panels which are shared between pairs of workstations. The floor is insulated, with polystyrene below the concrete, and in the tiled areas, the dark colour allows for thermal mass to accumulate. The roof has an R5 insulation value, with two metal skins and high-density polyurethane to prevent heat gain in summer and loss in winter.
The drawings of the building plans show a construction method akin to piecing a puzzle together, with the Birch plywood workstation units fitting into the structural plywood frames, which then fit into the insulation framing, and so forth. For the SGA team, who knows exactly what lies beneath every element of the building, there must be a sense of pride inhabiting it each workday.