Behind the Object: Te Aka Mātauranga
A 3D-printed pou – perhaps the first in the world – has been unveiled at MIT's TechPark campus. We caught up with Neill Laurenson, who devised the concept, about blending new technology with ancient design.
Manukau Institute of Technology (MIT) opened its new TechPark campus earlier this year as a hub for its engineering and trades programmes. With MIT sitting at the heart of South Auckland and bringing education and training to traditionally underserved Māori and Pacifika communities, Neill Laurenson – who is somewhat of a jack-of-all-trades with experience spanning from defence to construction to design – thought that creating the world’s first 3D-printed pou would be the perfect fit for the campus’ entry.
“TechPark is a modern trade school, so the idea of a 3D printed pou or ‘totem’ was to demonstrate, on a somewhat grand scale, the adoption of new technologies by MIT but still recognizing the old ways and cultural importance of who and what MIT is. The pou has both Māori and Pacifica elements to it, reflecting the nature of MIT’s students and staff,” Laurenson says.
After the initial idea and consultation with manawhenua and MIT’s cultural advisors, Laurenson assembled a team of artists and fabricators to help bring it to life. “We engaged master carver and kaumatua Ted Ngataki and his apprentice, Maaka Potini, from Ngāti Tamaoho to do the hand sketches. I then found a very talented young digital artist, Euan Craig, who is in fact and by chance an MIT digital art graduate.”
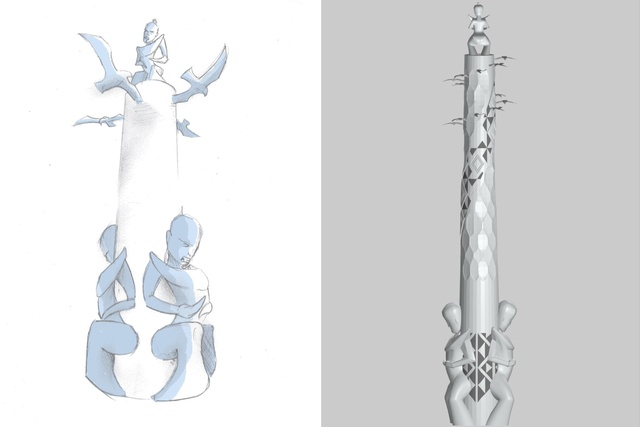
“The process involved a number of meetings between myself and MIT’s cultural team who were fantastic at adopting this concept as well as some really positive meetings with manawhenua leaders, all of whom fully embraced the idea from the get-go. It was amazing to see happen,” Laurenson said.
The design of the 7-metre tall pou features 12 birds circling its top, with Ranginui and Papatuanuku at the base. Ngataki noted the blending of old and new cultures, MIT reports. “The aim of doing it through this method was about the younger ones and opening their minds so they can think a bit more about the future,” he says. “We managed to uphold that side (tīkanga) of our culture in terms of the starting prayers, we always go through and the ending. All the stages of karakia we would use taking wood from the forest.”
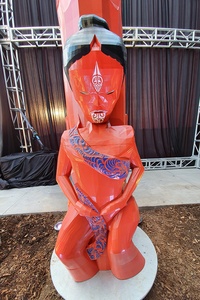
After the hand drawings were finished, Craig stepped in to create digital blueprints. The pou was too big to be physically 3D printed anywhere in New Zealand, therefore it was manufactured in eight separate parts by Melbourne company Objective3D. Laurenson notes that printing went on 24 hours a day, seven days a week and the whole thing took just over a month to complete. The parts were then shipped to Auckland and painted and assembled on site.
The end result looks like a traditional carved pou from a distance, but upon closer inspection, the pixelated nature shows through. “There was some design discussion about the final texture, but at the end of the day, the decision to make the pou still look as if it has been carved by ‘giant’ chisels, meant that the 3D printed finish worked in very, very well with the entire design intent,” Laurenson said.
MIT asked Ngataki how he thought the carvers that came before him would react to using new materials for traditional art: “They’d be tickled pink to see we are moving on. What I feel in me is all the rakau, all the Tane Mahuta are taken out of our land. We can’t go to that resource because of what has happened. It’s not right to use logs when there’s not enough left.”
MIT Deputy Chief Executive – Māori, Dr Wiremu Manaia also noted, “The pou has a story tied to Mana Whenua and is a symbol of the new direction of where things are going and how tīkanga Māori is evolving.”
See more from the Behind the Object series here…