Behind the Object: Wairua
Wairua is a new large-scale commission by Kiwi lighting designer James Russ. The piece, made for the lobby of Melbourne’s forthcoming Quincy Hotel, explores New Zealand’s place in the world and was created with brass that was pre-aged with a dip in Aotearoa’s waters. Russ lets us behind the scenes of the making of this piece.
How did this piece come about?
James Russ (JR): I actually exhibited my designs at Denfair in Sydney in 2018. While there, I met plenty of people including some of the designers for Toga Group – who are designing and overseeing the Quincy Hotel build. To be honest, I left Denfair feeling like it had been a waste of time. I was the only Kiwi exhibiting amongst a large and well-established Australian design scene. I didn’t think anyone there understood nor appreciated my New Zealand approach. Roll on two years later and I was asked if I would like to design and build the main lobby feature of an AU$90M hotel in central Melbourne. Who knew?
How did the idea for the design come alive?
JR: The idea was my reflection on the current state of humanity. Our lives are being turned inwards with the COVID lockdowns forcing our minds to travel rather than our bodies. I started to reflect on the places I had been to in my life and tried to find a way to map these thoughts and memories. It is not so much in an accurate “map” form, but rather, a way to represent how much impact and influence each place has had upon my life: The world as I see it day to day, from where I am now. There are so many stories to tell and I’m now wondering what life is going to be like without these influential journeys?
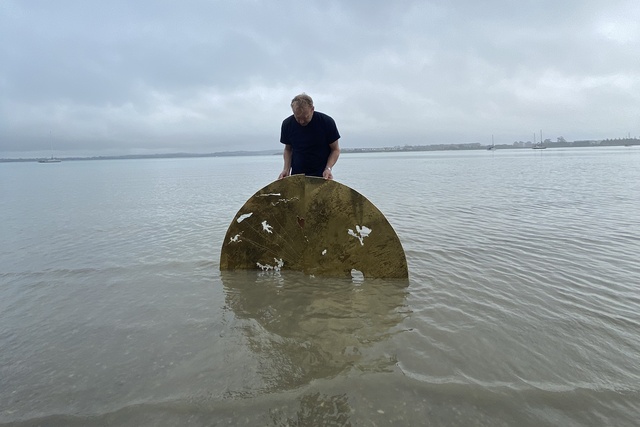
Did the idea for the design come inform how it would be made (which materials, the process, etc)?
JR: I wanted this concept to be represented in light. The scale, size and intensity of the light directly relating to the emotional impact of each location. I love the beautiful, textural detail of cast-glass, so I chose this medium to refract the light outwards towards the viewer. Brass sheet was chosen to encapsulate the overall layout. This is also surrounded by a soft glow of warm light. I love working with brass and knew that hand beating (using my father’s chisels – please don’t tell him!) these perforations would tell more of my story and provide an opportunity for “happy accidents” along the way.
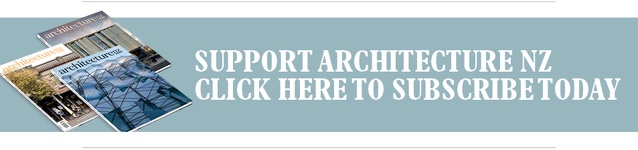
Give us a step-by-step of how the piece was made.
JR: Although I’m trained in industrial design, I much prefer a hands-on development process. Here’s a bit of a timeline:
1. Initial concept pencil sketch and written explanation.
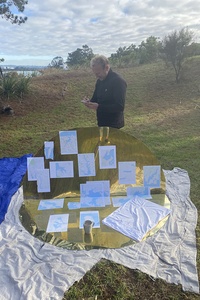
2. Prototyping of a small section of the sculpture to convey the “light perforation” effect. This was made in hand-beaten brass and using opalescent wax to represent cast glass and transmit light.
3. Materials purchasing. This is worth a mention as the irony of sourcing brass sheet in New Zealand is that it comes from Melbourne. We buy the brass from there, it gets sent to us, we beat it up, then send it back. I never mind this approach though as I’ve always aimed to create objects that will last for generations rather than multiple, lesser-quality objects that will essentially end up in landfills.
4. Then I worked on the object in full scale. As all the perforations relate to either harbours or landforms, I needed to mark these out in reverse on the back of the brass sheet. This was a real brain-teaser especially, as you’ll read soon, when mother nature starts to modify things.
5. Once all the sculpting was complete I had help to take the brass pieces down into the sea, in the exact location that is represented in the centre of the piece. It was a rather spiritual moment, gently washing the saltwater and dark sand over the brass adding to the already rich patina.
6. The next stage was pouring molten wax into the perforations. These become moulds for the lost-wax glass-casting method. Some of the glass pieces are over 2kg in weight so the glass kiln ran for a full week to ensure the result was exactly what I was looking for.
7. The final stage was adding the LED light. Differing amounts of light were added and dimmed to convey the soft effect that I wanted.
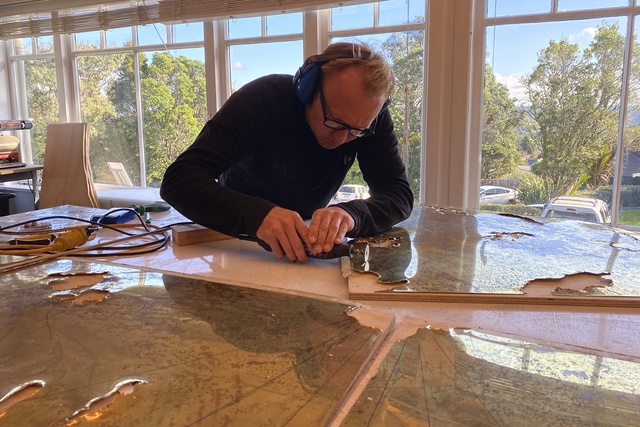
Was there a trial and error process? Did you face any unexpected challenges along the way when developing the item?
JR: As the sculpture was too large to build inside, I started to build it outside on a densely-packed bed of sand. Each night I would lovingly cover it up and the next day work away on it again. This method worked perfectly well to preserve the glossy brass look until one weekend when a vicious North-easterly storm arrived. This storm ripped away the cover and completely ruined all my layout markings. The rain had also soaked upwards through the salt-laden sand completely changing the look of the brass.
I was in disbelief until I realised that the natural patina effect was truly beautiful. There is no way that I could have intentionally produced such a lovely, dynamic and deep patina effect. Mother nature can be very kind sometimes.
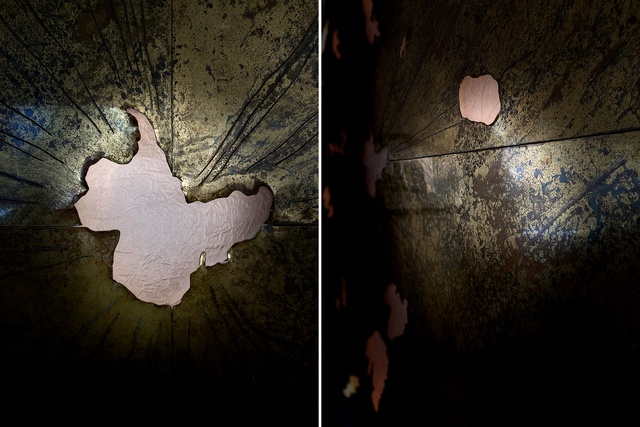
What are your thoughts about the final piece?
JR: It is worth mentioning that every facet of this project has come together perfectly. And, I had great help from my small, talented team along the way. Although I’m essentially exposing my most personal thoughts with this piece, it feels like I’m channeling a concept that has always been with all of us. That is why I have called this piece “Wairua” – Spirit of a person.
See more from the Behind the Object series here.