Elegant toolbox
Lifting the veil on the APL brand was a key objective in this technology-led fit-out. Joanna Jefferies steps into this surprising and award-winning factory in Hamilton.
APL is renowned across the architectural industry as a big player – their aluminium joinery is specified in projects across the country and their technology is cutting edge. They are also a New Zealand, family-owned business, and are widely known for their support of the architectural community, its events and awards. So when APL approached Jasmax in 2014 about a new project they had in the pipeline, the response was enthusiastic.
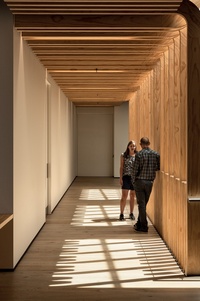
The project was a new build – essentially a large warehouse structure of 4,600m2 situated on a high-profile site across the road from the original APL building, in an industrial area adjacent to a main highway in Hamilton. The building was to house three business entities: it would bring together APL’s design and innovation teams into a single office space with adjacent workshop and testing facilities; PPL’s plastic profile extruding and product testing; and IML, the distribution arm for aluminium extruder Inex. Creating a physical connection between the three departments was key.
In an initial interview between Jasmax and APL, Jasmax principal Nick Moyes was taken aback by the unconventional brief. “We started off by saying ‘we don’t do factories’.” But he quickly realised the project was much more than an industrial shed: the finish and spec were to rival a high-end residential interior, and experimentation with APL’s latest technology (not typically seen in an industrial space) was a key objective.
APL commercial systems manager Jason Lawrence says the new building is an opportunity for APL to create a gateway to the brand, given its high-profile location. It also unites the design and innovations teams within APL, giving them their own collaborative space, while still maintaining their connection with the manufacturing and trading sides of the business.
The ground-floor entrance and stairwell, which welcomes visitors into the heart of the space, certainly attests to this objective. Steel and polished concrete are the key anchors of this space, with strong timber elements employed to soften and contrast.
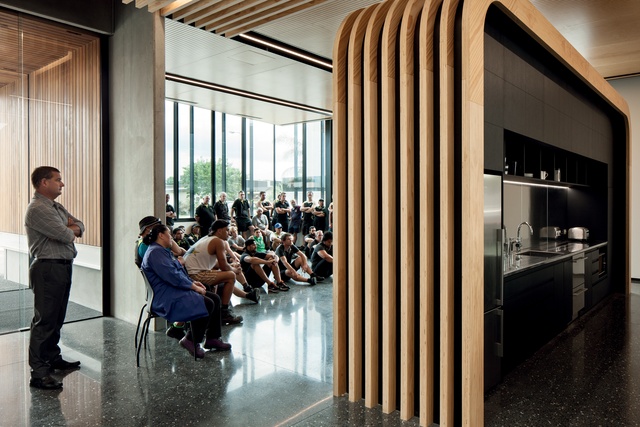
The entry circulation area creates a ‘doorway’ to the brand – its timber ‘fins’ suspended from the first-floor ceiling (APL designed a bespoke hanging system) break up the volume of space created by the floor-to-floor heights of five metres. Timber detailing lines the ceiling in the form of battens and embodies the trope of ‘componentry’ that is central to the APL brand. The language of the timber battens is extended via the sculptural ‘fins’ and creates continuity in the space, connecting the offices on the first floor with the events space and staff cafeteria below.
A wall of glass behind the oak stairs spans the two floors and fosters interconnectivity between the offices and workshop, which allows the design and innovation team a bird’s-eye view into the testing of new products. The first-floor offices employ a matte, clean, neutral palette with timber accents, reflecting the slick aesthetic of APL’s products. Jasmax senior architectural graduate Greg Hughes says the key was to restrict the palette and to achieve a very high standard of workmanship. “You’ll struggle to find a level of finish like this in a high-end residential home,” he says.
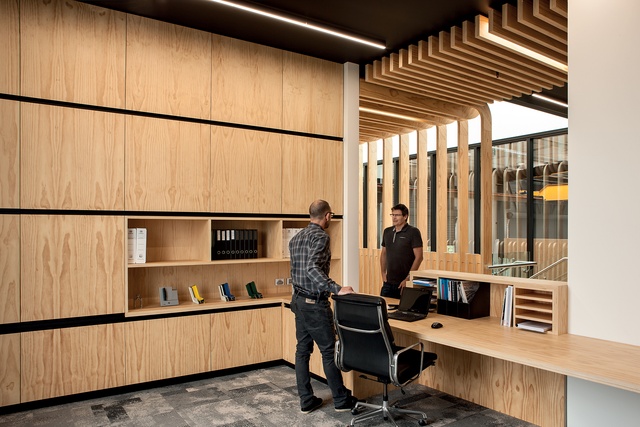
Therefore, the detailing is bespoke throughout. The aluminium joinery and glass walls of the boardrooms sit flush with the plasterboard (a design engineered by APL with the intention of trying it in the new space), creating an elegant negative detail. This tailor-made detailing meant the plasterboard had to be installed after the joinery and skirting were in place. The full-height ‘pivot’ door into the offices was another chance to play with design.
The design and innovations teams were able to be part of resolving technical issues and creating bespoke solutions during the build process. Comfort is taken to the next level in their shared office (which gently divides the teams through the use of a storage wall with in-built plywood shelving).
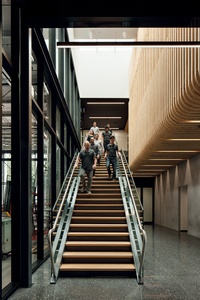
The double-glazed twin-skin glass façade creates a cavity where the air supply can be moderated before it enters the office space. The air supply is drawn through underground earth tubes, where the air is conditioned and moderated by the ground temperature before it is fed into the glazed cavity. Blinds inside the cavity help to control solar gain in the office and at certain times the cavity’s internal doors can be opened to naturally ventilate the office space.
“The office spaces themselves fundamentally don’t have any air-conditioning or heating in them. [APL] were looking to control that indoor environment through the way that façade system operates – really testing their products to change the way the office spaces work,” says Moyes.
They certainly weren’t after another ‘shed’ with this level of sustainable technology, says Moyes, though he admits there is an elegant juxtaposition between the raw industrial mechanics of the workshops and the slick detailing of the office space. “It’s the most beautiful toolbox I’ve ever seen.”
STRIKING LIGHTING
The façade of the building had to create a powerful impression to grab the attention of passers-by – especially people driving past at high speeds, according to Jasmax’s project principal Nick Moyes. “The architectural mood had to be clear and simple, but bold.”
This is accomplished by means of LED lighting situated within the louvres of the building’s exterior. The daytime activity within is visible to people on the outside through detailed louvres that move along the 110-metre-long face of the building. At night, the façade is transformed by colourful LED lighting that can be changed at a whim.
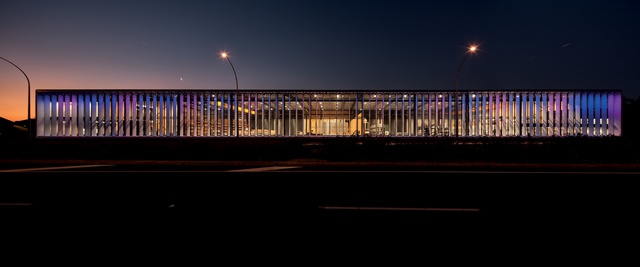
“By being able to change the colour of the lighting when and as they please, APL has a mechanism to speak to the community about different things,” says Moyes.
“The original idea was to decorate the frontage with a 110m photograph, but after no one could decide what the photograph should be of, it was decided to use LED lighting.”