Lucas House and Upper Queen Street buildings
It seems that Nelson is not just a sun-drenched land of hops, fruit and bronzed, blonde German tourists. It is also firmly leading the country – perhaps even the world – in the art of using massive slabs of timber in clever seismic structural solutions.
It all started back a few years ago, with the hugely innovative and multi-award-winning timber building for Nelson Marlborough Institute of Technology (NMIT) (featured in Architecture New Zealand, 03.2011). That used large, structural timber LVL columns, beams and shear walls, structurally post-tensioned using cutting-edge technology for energy dissipation, with architects Irving Smith Jack (ISJ), engineers Aurecon and the University of Canterbury all working together to test some ground-breaking solutions.
Timber/concrete composite floors, using the Potius floor system, provide mass deadening for acoustic and fire reasons and the structure became the first of a new breed of damage-avoidance buildings, all built by Gibbons Construction. Let’s call the NMIT building Generation 1: like Noah and his wooden Ark, it has spawned a whole world of new offspring.
What is presented here today, is Lucas House (Generation 2) and two buildings in Upper Queen Street: TB1 (Gen 3) and TB2 (Gen 4). And right now, the laid-back Nelsonians at ISJ are preparing themselves for another exciting big timber building number with Scion (Gen 5).
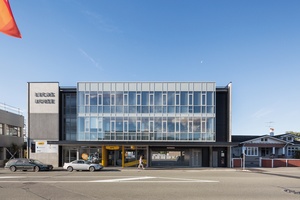
Let’s take it one step at a time. Lucas House, three storeys high in the centre of Nelson, has tall, boundary pre-cast-concrete shear walls. Nothing unusual, here – from the outside. Inside, though, this building really rocks. No, seriously, it really does – or will – when the big one hits the Tasman district. There are seismic precedents in the region, of course: the 1929 Murchison ’quake knocked down half of Nelson and the 1968 Inangahua ’quake made the remnants wobble.
If you’re anything like me, you may have been fairly horrified by the amount of apparent needless destruction in Christchurch, with demolition of seemingly undamaged buildings taking place long after the event. Lucas House, however, is ready to fight the next one and come out smiling via Aurecon’s engineering and PRESSS technology. On the inside of those tall, concrete side walls, complete with Macalloy post-tensioning bars, the base of each plank of pre-cast is bolted down to the foundations with massively chunky dampers and seismic ‘fuses’.
These over-sized steel shock absorbers will hold the building onto the ground, soaking up the rock and rolling of the big quake, absorbing the energy into the fuse, and then settle the building back down, with next to no residual damage. The damage-avoidance strategy is to allow small parts to be replaced (i.e. the steel fuses within those large metal cylinders) while the building comes out unharmed.
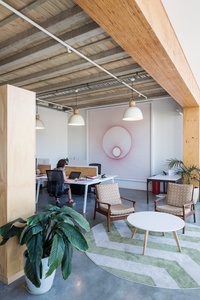
Inside, LVL columns and beams support a concrete Interspan floor resting on a timber corbel. There’s no real structural reason why the floor couldn’t be all timber too, but concrete was deemed necessary for acoustic, fire and other reasons. Air conditioning is largely absent – despite the intense summer heat on the day I visited, the offices are comfortable – as the building is designed to be ventilated mainly naturally, with sensibly large protruding ledges providing the shading, and a veritable plethora of opening panes to front and back. This is a good thing: an honest, simple, modernist office building, done well with wood. Next please!
The genesis of the next project was a lot more complicated but is a refreshingly positive tale. In nearby Richmond, the fast-growing little sister of the more well-known Nelson, the town seems to be in love with big-box retailing. As we all know, ugly normally comes as standard with the big-box typology, often coloured bright red or lurid orange.
Faced with yet another big-box development, replacing an elderly PlaceMakers site, Tasman District Council (TDC) decided to hold a competition, in the vain hope, perhaps, of securing a better treatment of the boxy elevations – coincidentally, directly in front of its TDC offices. ISJ won the job, working again with Gibbons and, in a serendipitous piece of scope creep, has become the architect for what may well be the best-looking big-box development in the country.
The big-box barns are, of course, just the bog-standard formula fit-outs for Kmart and The Warehouse, composed of long-span steel portal frames over perfectly flat concrete floors. Amazingly, this Warehouse is not a painted Red Shed (although, in this case, the community wins: everyone gets a bargain).
The front façade of this retail haven is a work of beauty, almost, and certainly a step up from the painted metal walls of the typical retail barn. ISJ has inserted a frontage of small retail shops between the two major tenants, and so created a pleasant pedestrian zone. A tasteful timber louvre screen above the entry doors works to create a carefully modulated and tastefully proportioned parapet walkway.
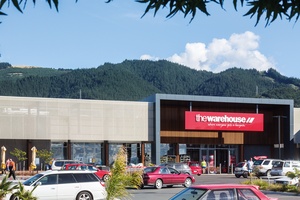
But it’s the side road where the architecture really shines through. The TB1 (Gen 3) building flanks The Warehouse and plays the same sort of clever timber tricks as does Lucas House, although with more refined details, courtesy of engineers CDT Consultants. TB1 has dispensed with the concrete structural side walls and gone for a fully glazed box, with internal timber shear walls (a mix of CLT and LVL) proudly on display. These are held up above the slab by relatively slimline devices, which, intriguingly, are simply screwed onto the outside of the timber shear walls and bolted down to the ground slab, with easily replaceable steel fuses within a slim epoxy-filled tube.
On these Upper Queen Streey buildings, ISJ worked with Nelson Pine to cut out carefully a nice recess into which the concrete Interspan beams could sit nicely. Next door, TB2 goes a step further, with an invigorating timber/concrete floor system, masterminded by the University of Canterbury’s Alessandro Palermo and Stefano Pampanin. Timber columns and beams slot together almost invisibly, bolt fixings all hidden within. The buildings will rock and return to their positions, unharmed, after an earthquake. The concrete-marketing organisation CCANZ must be worried: I think that this timber building is the future.
The buildings hold the street line with a series of angled louvre screens to shade the northern and western façades, and celebrate the three major openings into the buildings with tall portico entries, one of which opens directly out to TDC’s Richmond Office. Hooray! Townscape returns! It offers a vastly more refined and hospitable solution than does the side of a giant tin shed, and it seems the tenants agree – not only have the smartest lawyers in town moved in upstairs but even The Warehouse has taken some space for its own offices.
One hundred and forty years after architects Stead Ellis and William Beatson started building with timber in Richmond, we have some good wood again. It’s good urbanism, good townscape and good, competent architecture. Unlike the adverts for the companies on TV, the building doesn’t shout at you. It merely sits there, quietly content to be ground-breaking and wonderful. Roll on the timber revolution!