Not your typical architect
With over five decades of experience, John Sutherland reflects on some unresolved issues over a long and multi-faceted career.
Not your typical architect. Not really an architect at all as one of my wife’s friends – the wife of an architect colleague – maintained some time ago. Why? Because I didn’t design buildings like her husband. I had. But this is not about spelling that out in a defensive sort of way. In short, I designed very little during my time at JASMaD/Jasmax.
But what that includes depends on where one’s view of design stops and something else takes over.
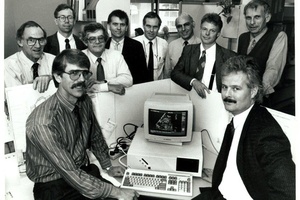
There is no doubt that my career did not straight line in a traditional way. It veered off into all kinds of opportunistic things to do with architecture, always driven by the importance of process and a firm belief that architects needed to become more interested in getting their buildings built or someone else would take that part of our work from us as others largely have.
I saw the procurement process as the all-important part of the design process. I have always believed that architects needed to get closer to the supply-side and understand its part in achieving our design ambitions. Little did I ever think I’d still be in practice at 86, which either shows a lack of initiative or that it’s been an enjoyable ride – the latter actually.
It was early 1966, when I joined JASM, before it became JASMaD, when all my strange architectural interests started and were allowed to develop.
Technical literature
The quality and usefulness of technical information about building products available to architects in the 1960s was appalling. It was mostly produced by advertising firms that didn’t have a clue about what was needed. The New Zealand Institute of Architects (NZIA) Auckland Branch and the Auckland Building Centre decided to run a Trade and Technical Literature competition after a London Building Centre model, as a way of improving matters. I was put up as one of the judges, and we found good reason to be very critical of most submissions. Things did not improve much for the following year, with the same critical result.
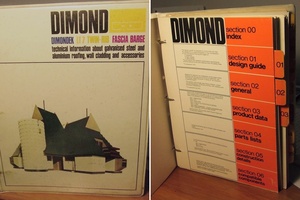
As a result, JASMaD was asked to take on a couple of commissions to show how it should be done and what was really involved. Over a short time those commissions built up, and JASMaD Information was established as a profit centre to carry out this work, effectively becoming a technical advertising agency.
We found ourselves networking with similar groups in Australia and the UK. We hooked into “BS 4940:1973 Recommendations for the presentation of technical information about products and services in the construction industry” and got this document cited in the appropriate product and component New Zealand Satandard (NZS) of the time.
This didn’t last long [into the 1980s], but our documentation was popular with architects until our clients decided large, paper-based literature was too expensive and the digital age arrived. Today it is generally available with one click of the mouse on Google. Information availability and accessibility is now amazing. For many the goal is a paperless office!
Building industry conservatism
My experience in architectural practice led to a firm belief that the industry and its welter of neatly siloed participants (including architects) were using outdated Victorian methods of very traditional project delivery and were not serving their clients well. My view has not dramatically changed, as the industry has also not changed positively.
My interest started in 1961 when I happened upon an Edinburgh University MArch thesis that developed a theory of structured project documents (working drawings). By 1962 I had already used it once, but found it too extreme.
I wanted to do something about it and did, by practicing what I believed in, by being an educator, a writer and a travelling Cassandra, warning/advising my colleagues in the industry that there was a need to change their ways.
Early on, I was very influenced by the 1966 Tavistock Report, Interdependence and uncertainty: a study of the building industry. This was a piece of operational research on the United Kingdom building industry and strongly resonated with what I was finding in New Zealand and Australia at the time.
Recognising that the United Kingdom building industry had problems serving its clients well, there have been a plethora of reports commissioned by governments, all building on Tavistock’s unpeeling of the onion. They all – especially reports written by Banwell (1964), Latham (1994) and Egan (1998) – agreed that the main problems were the structure of the building process that all the inmates wanted to follow.
Building in New Zealand and the United Kingdom happened in the main by a slow, linear process with a strange preference for adversarial contracts at all levels, and where the parties didn’t actually engage in any meaningful dialogue early enough. It was a process which advocated for unalloyed market forces, leading to an industry with a culture of ‘lowest price wins’ where, if someone wins then someone else loses (no win/win allowed). This, in turn, lead to tiny profit margins for all and an unstable industry
It was pretty old fashioned. Even in the 90s I believed what was needed was early contractor involvement (ECI), teamwork built around sound IT leading to building information modeling (BIM), collegial behaviour, sensible risk allocation, openness, more acceptance of new ideas and ways of doing things, including trust: all leading to mutual benefit. Everybody wins. Sadly, this alternative was deemed too hard.
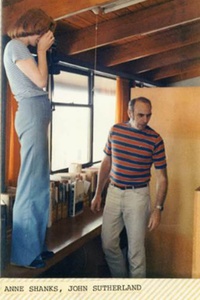
The problems are still with us. I know I have failed. That worries me. There are just too many vested interests believing in maintaining the status quo. However, as is well known, if one does the same thing, one gets the same result. The building industry is replete with this kind of activity and thinking. It is just too busy and too underfunded at all levels to do anything else. It believes it can’t afford to stop and think.
What that tells me is that our way of doing things twenty years on since Egan is not much different and that no reports like any of the United Kingdom examples above have ever been commissioned in New Zealand. Governments have taken a hands-off approach once the Ministry of Works got dismembered in 1988, leaving the gathering disaster to the market to sort out, which of course, it can’t.
Strangely – should I be surprised? – the problem is getting worse as the collective of a proper project team has been broken up in a way that cannot be put back together during the life of one contract. This is largely because of poorly allocated risk and often incompetently assembled teams. The industry has now become so risk averse that industry-wide constipation has set in. Nothing moves. Not even small risks can be taken, so the tried and true must be followed even when it is often accepted as not really working in the design/build and novated contract climate of today.
I believe that clients are getting poor advice, leading to poor outcomes. But, for some part of that failure they share responsibility because of unreasonable expectations of the building industry.
Lawyers and project managers
Clients believe that lawyers will save their skins by one-sided contract drafting. Lawyers, not really understanding building, alter standard conditions of engagement or write unique documents – both with so many special clauses that architects then must employ different lawyers to advise them on what to fight over, and that’s before design has even been contemplated.
The whole circus is then re-litigated about the construction contract, but now involving contractors, subcontractors and the liabilities of architects and project managers. Attempts to introduce collegial contacts such as the mistakenly named New Engineering Contract (NEC) suites have generally foundered because lawyers, project managers and, to my despair, even architects and the Joint Contracts Committee (JCC) do not want to use them, being too different.
‘It ain’t really broke, don’t change it’ is the usual cry. But it is broke! It is easier to spend much energy and resource massaging and polishing their adversarial forms. However, apart from lawyers and project managers, for the design team itself to innovate and recommend new and different methods is seen as likely to invite a claim later. So, don’t do it.
For architects the problems started in the late 1970s with the appearance of a bunch of people without qualifications who collectively chose to call themselves project managers (it not being a protected title). They saw an opportunity to take over, for would-be clients, parts of the sequence architects didn’t like doing much or did rather poorly. This included, typically, knowing what their design was going to cost against the briefed cost, what the finished cost of the building project was going to be and then managing the overall process including variations, increased costs, requests for information and time extensions.

Quantity surveyors stopped contributing positively either and for a time were advised by their Institute to become project managers. Quantity surveyors have now seemed to position themselves not as part of the team, but as the client’s watchdog, driving value engineering. Not that the process can be very beneficial when done sensitively. Rather than doing something to counter this, architects dropped the ball and didn’t pick it up again. We are still not good at pushing back. If we are not careful we will become concept and design providers only: others, for whom design integrity is not an issue, will take it on from there.
The 1980s brought the forced abandonment of all institutional fee scales – which Sir Miles categorised as “the Sutherland falls”– and knowing the cost of doing business, and most importantly, how to calculate a competitive but adequate fee for the work to be done, became imperative. Over time and under this regime project managers thrived and architects wilted.
Project managers and design managers as a subset (with some exceptions) have now positioned themselves in a way that it is very difficult for architects to talk directly to their actual clients: to get to talk about non-adversarial contracts and better collaborative ways of doing things as an alternative to hard-nosed ‘divide and rule’, often conflicted and fractured, methods preferred by project managers.
Just recently former Australian Institute of Architects national president and chief executive Michael Peck was quoted, noting how in Australia while the law imagines “a continuum of architectural services from design through to the completion of the building”, the reality is one where responsibilities are obscure and fragmented. Rings a bell?
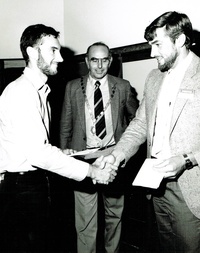
Consequently, the NZIA still seems rabid in believing that in defending the position of architects in the firmament by offering ever more awards, nothing really needs doing, even in the face of some recent industry-destroying failures. My soundings in the industry tell me that architects do not have a good reputation in today’s industry with regard to providing comprehensive, complete, accurate and helpful documentation for the contractor.
NZIA architects seem borne down with risk but on the recommendations of others, prefer (or are required) to operate with adversarial contracts (which actually create more risk), leading to traditional procurement processes, which actually are unsuitable for what’s happening around them.
I have been banging on about the need for better communications between participants ever since 1968 when a bursary from Winstones and a scholarship from the University of Auckland School of Architecture allowed me to research and report on current practice in both Australia and New Zealand.
To do better than being just a watcher or commentator, I have had the opportunity of putting into place contract procedures that did something about some of these problems. For example, JASMaD ran two projects for Vacation Hotels in Rotorua and Auckland under one “Managing Contractor” fast track contract using one set of steel formwork that moved from one city to the other.
Another for the Arts and Commerce project for the University of Auckland had three carefully defined parts project managed on a labour resource basis by a newly established firm of “poachers turned gamekeepers” chosen by us. A further example was for the Majestic Centre in Wellington where the developer put the contractor, subcontractors and all the design team together in a cupboard and threw away the key saying: “Just deliver me a building. You will fix everything between yourselves.” It worked until the developer itself went broke, as did its successor, the financier.
For me everything came to a climax on the Te Papa Museum of New Zealand project where Jasmax and Carson Mills – the Project Manager selected by us – recommended a procurement process of construction management of about 25 separate contracts under partnering and quality assurance procedures to the Museum Trust Board. This meant no main contractor as all subcontractors were effectively contracted to Her Majesty the Queen.
All these were examples of procurement-method driven design and construction-method processes. Drawings and specifications were produced according what was needed to be bid or built on site. All the better methods I had been researching and using came together on Te Papa and with Carson Mills we found they worked, contributing to successful outcomes for the clients.
All these projects were supported by the JASMaD developed (and later sold to the industry) Masterspec and its CI/SfB (later CAWS) elementally structured documents. These had been developed working with Royal Institute of British Architects (RIBA) Services and its National Building Specification (NBS) division in the United Kingdom and within the developmental work of the Conseil International du Batiment (CIB) W 78 ‘Building Industry Information’.
I travelled throughout New Zealand in 1972 lecturing to NZIA branches on ‘Data Co-ordination and Project Documentation’: effectively, on the benefits of using CI/SfB elements for structuring drawings, office libraries and specification sections. I was received with some polite but critical, if not antagonistic, interest and only a few takers – albeit some significant ones, like the Ministry of Works and New Zealand Breweries. Nonetheless these methods – changed over time to match the information technology available – had served JASMaD/Jasmax well since 1968. It is now BIM, IFCs and Revit, not CI/SfB elements.
Windows/claddings and weathertightness
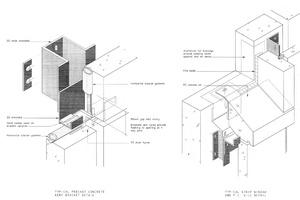
One of the JASMaD directors had given a talk to the New Zealand Joinery Manufacturer’s Federation (JMF) annual conference in 1967 about the joys and benefits of using timber windows. Usually that’s it, but this time a deputation of senior joiners turned up early in 1968 and asked us to design a new window system to compete both with the standard timber window profiles of NZS 3619, which were profligate with timber and the burgeoning use of powder coated or anodised aluminium windows.
On the way to the ultimate collapse of JMF NZ Limited over 25 years, JASMaD ran a small team of industrial designers and architects who set about reconsidering every kind of window type it could think of. Working from overseas documents (until NZS 4211 arrived) we tested everything we built for weathertightness and structural performance.
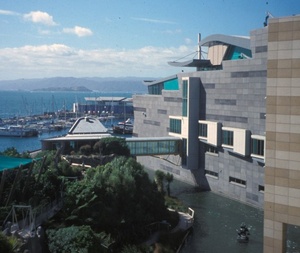
We very quickly became aware that success (compliance with performance targets) was very dependent on airseals, robust hardware and better finishing systems, none of which were readily available except for the Interlock friction stay. The idea of airseals at the back of the sash was foreign, if not anathema, to the very conservative and traditional sub-contractors we worked with, but were vital in the competitive war with the aluminium window industry who were already running back-sealed pressure equalised window systems. It took until 2005 and the new E2/AS1 for window frames to be installed into openings with back air-seals all round creating a full pressure equalised system fully integrated with the new drained and ventilated cavity cladding systems.
As a result of working for JMF, I found myself also working with the Architectural Aluminium Association of New Zealand (AAANZ) as a technical consultant and writer and worked with both on a standards committee to help produce the first version of NZS 4211: 1979 Performance of Windows.
For the JMF I lectured joiners on ‘The concept of specification by performance’, for AAANZ it was ‘Windows and Standards’, plus producing three versions of The Aluminium Window Handbook for designers and developed specification sections for Aluminium Windows and Aluminium Curtain Walls for the Handbook which ended up in Masterspec in the mid-1990s after Jasmax had sold Masterspec to the building industry.
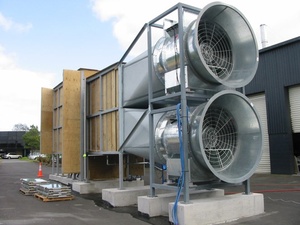
Over 50 years, I have delivered forty two publications and presentations to a wide range of local and international building industry groups. The best known internationally were two frequently cited papers: Façade Design and Procurement, presented in 2003 to a Centre for Window and Cladding Technology conference; and Building envelope technology, presented in 2007 at the International Conference on Building Envelope Systems and Technologies. Both papers were on New Zealand’s leaky building syndrome, which to some extent was caused by the light regulatory intention of the first Building Act (BA91), combined with some industry incompetence which had developed over many years.
These problems were hopefully to be solved by a new dose of regulation in the second Building Act (BA04) and are described in the second paper. The optimism may not yet have been fully realised, but any problems seem to have been prevented by a general uptake of performance tested cavity constructions to create compliance with the New Zealand Building Code itself – not just the significantly expanded Acceptable Solution, which appeared in 2005.
This is just the half of it. It’s been a long two-way process based on international and local networking. Out of it all came learned-on-the-job expertise and, I suppose, relative expert status in New Zealand, built partly on strong and useful process connections locally and overseas. There have been many career reinventions. Each has come naturally from what went before but always supported by my long- term involvements with many aspects of an NZIA/JASMaD/Jasmax lifetime.
Looking back I can see that my 30-year JASMaD career, punctuated by seven years of part-time academia in the mid-1980s teaching and researching architectural practice and process, enabled my dual roles on Te Papa and resulted in my reinvention as the foundation Head of the Unitec School of Architecture and teaching weathertightness construction. That, in turn, allowed another reinvention, this time as a façade consultant for eleven years with Aurecon and Mott MacDonald.
It’s been a matter of being in the right place at the right time and always saying “yes, why not?”, and then doing something new and different. As a process, I can recommend it. The most recent reinvention has been returning to Jasmax in 2017 as a technical consultant, using all aspects of my experience: in short, ‘back where I belong’ as my business card says.
Perhaps it should have said “not your typical architect”.