Ohakea: five star facility
The RNZAF's new maintenance facility gets top marks with its five star green rating.
An orange tower has appeared on State Highway One, between Sanson and Bulls. The parachute washing and drying facility signals the growing presence of a new Maintenance Support Squadron (MSS) complex at the Royal New Zealand Air Force’s Ohakea base. On completion the RNZAF will move into 14 industrial (predominantly aeronautical) workshops, as well as offices and stores in the purpose-built facility.
The old buildings are WWII era buildings – constructed between 1937 and 1950 – and have outlived their use. They will be demolished to make way for a new air passenger and cargo terminal as part of five infrastructure upgrades. Wing Commander Peter Neilson says the new facility will be comparable to the Air New Zealand engineering support workshops in Auckland but with more focus on military support and the workshops’ capabilities will be relevant to all three services.
“The new workshops will provide improved facilities in specialist areas such as hydraulics, non destructive testing, life support, and cargo chutes, as well as composites, aircraft and vehicle finishing and component manufacture,” says Neilson. “The new building is designed to have a high specification environmental management for areas that have strict health, safety and environmental discharge requirements, as well as very precise technical standards to maintain work quality and standards.”
Mainzeal started work on the complex and the associated aircraft finishing section (AFS) in January 2011. Project manager Callum Harvey says it will be a five star facility, and the stars apply to the building’s targeted Green Star rating, as well as the overall quality of the design and construction. Don Gillies, Mainzeal contracts manager central region, says the Green Star rating system adopted for the project is the Industrial 2009 Rating tool and the MSS is the first building in New Zealand to be constructed to this standard.
“Out of the eight categories in the five star rating tool is classed as ‘New Zealand Excellence’ and Mainzeal is currently targeting the required points to achieve this rating.” The move to environmentally sustainable designed (ESD) buildings makes sense for NZDF, says Neilson, because it usually owns and occupies its buildings for longer than other landlords and/or tenants. “We adopted the principles for ESD as espoused by the New Zealand Green Building Council (NZGBC). The principles require consideration of indoor environment quality, energy use, transport options, water consumption, material selection, ecology, emissions, building management and building innovation,” says Neilson. “The benefits to NZDF are lower whole of life costs and a better working environment for the buildings’ occupants.”
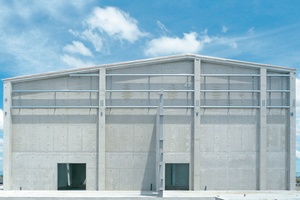
The MSS building, 206 metres long and approximately 54 metres across, will have the largest footprint of any building constructed on a New Zealand Defence Force camp or base. The building is constructed inside and out using precast panel wall components, supported on a steel portal frame structure. The metal clad roof will have access ways to service roof-mounted mechanical services. “While visually tall and long, the architect [Aecom] has used the roof forms and access points to minimise scale and humanise the building,” says Gillies.
We began our site visit at the north end where the 23m tower stands. The massive parachute washing and drying facility is the first to be built in New Zealand and cleans four parachutes at a time. The parachutes are those used when Hercules aircraft drop cargo from the air. The tower has to withstand 160 knot winds and is firmly anchored to the ground by a 300 cubic metre mass concrete foundation pad. It’s massive because of the weight and height of the tower above it.
“The wind loadings out here are excessive,” says Harvey. Underground, the presence of a riverbed and water table at one and half metres meant they continually struck water when excavating for the works. “We just dug a well beside it and pumped the water out. It was unpredictable though. As we progressed down the building the water would go away, next stage it would come back.” Harvey says to construct the parachute tower they erected the steel structure first. Then, rather than using a scaffold, they craned up all the external cladding along with a man-cage work platform. “Obviously working around the weather – but it ended up being faster because of the cost of the scaffold against the cranage and the time.”
A chamber is built within the tower steel structure, insulated and completely lined with Kingspan panels. Mainzeal built the chamber from a birdcage and pre-stacked all the materials inside, such as the nine to 11-metre long Kingspan panels, before erecting the scaffold. To dry the parachutes, air is sucked into the chamber from the top and blown down through the side shaft, in through the bottom grilles and then sucked out, like exhaust, through the top. During a walk through workshop spaces, offices and staff facilities under construction, immediate points of note were: the massive Steltech beams that span up to 28 metres across the workshops, large amounts of acoustic and thermal insulation installed above and below the roof purlins, multiple cable trays, services ducts and cabling – all very visible under the many double-glazed skylights that let daylight into the building.
Services for the MSS and AFS buildings represent 45 percent of the total cost of the project. There is compressed air in every workshop, over 150 air-handling units; duct work and fans overhead. Extra data and security services have been added to future-proof the building. “It’s like a hospital for maintaining all the helicopters,” says Harvey. Made up of a massive steel frame and metal and concrete skin, wrapped in huge amounts of insulation and lit during the day by natural lighting, the building will be robust and operationally highly energy-efficient. The internal environment will be controlled by the Invotech building monitoring system (BMS), which Aecom has designed. It will monitor the energy efficiency of the building, water and power usage (water is collected from the roof; energy from solar panels heats the water). The BMS will regulate lighting, airflow and temperature. Gas fired radiant heaters will allow additional heating to be individualised.
Fibreglass insulation was being packed into the roof and walls – 150mm framing, along with two, sometimes three layers of 13mm acoustic insulation board. The connecting spine corridor will be heavily insulated and was “nogged out” halfway up the wall for the installation of acoustic baffles. Craig Irwin is Mainzeal’s area health and safety and Green Star manager. To meet Green Star requirements in the materials section he says they have poured 3100m3 of concrete on site, 20 percent of which has been replaced with recycled concrete aggregate and 28 percent of the total figure replaced with flyash waste products. The amount of PVC used is minimised and replaced by other materials. For example the electrical cabling on site is sheathed with rubber rather than with the convectional PVC sheathed cables.
All construction waste generated on site is removed by the waste management contractor and recycled where possible. Currently 96 percent of the waste generated on site has been recycled including scrap metal, steel and other products such as plasterboard, cardboard, plastic, polystyrene and so on. All of the structural steel contains at least 50 percent recycled; the reinforcing bars used in the slab and foundations of the building are made with 95 percent recycled content. “Leftover treated timber goes to the aid group Focus Humanitarian Assistance where it gets sorted and shipped overseas to build houses,” Irwin says. Paints, silicones and sealants have a low VOC content which will allow better air quality inside the building once it is constructed.
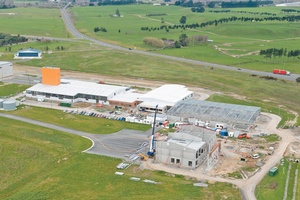
Fire protection is a critical factor in the health and safety of the facility and is catered for by three fire cells, with two associated seismic joints; all the services are passed through the firewalls; the entire building has sprinklers, however each workspace is an individual room. “If there is a fire in one room it won’t activate the sprinklers throughout the building,” Harvey says. All the structural steel firewalls are sprayed with intumescent paint on site and then tested for the correct micron cover.
Mainzeal began construction in January 2011. During the early stage of the works the mechanical services design was revisited and changes to the heating system have pushed out the completion date. A decision to replace steam with gas brought more sustainable efficiencies. “The only downside is that the flues go through the roof and increased the number of penetrations we had. It’s all watertight at present but we have to put in the roof penetrations yet – they are all pre-marked,” Harvey says.
Underfloor insulation was also changed from pumice sand to polystyrene. The pumice lost its thermal barrier properties when crushed and trucking it from Taupo would have increased carbon emissions. The AFS or aircraft finishing section next to the MSS building is an aircraft paint and panel shop built to contain a complete NH90 helicopter and Kingair fixed wing aircraft. Complete CT4E air trainers and A109 helicopters will be painted in the AFS facility; parts of other aircraft will also be painted in the smaller specialised paint spray booths.
The AFS building is constructed on three sides from 150mm thick self-compacting concrete walls 12 metres high poured between precast columns. It has a free span concrete ceiling to the aircraft spray shops which double as a plant room floor for three large air handlers that recirculate air to the aircraft paint shops below. The front of the building includes access doors and an air chamber, which receives the air from the large air-handling units for the paint shops.
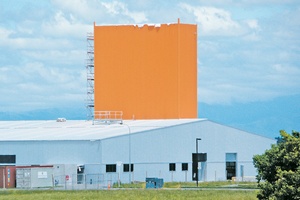
“The ventilation system is on a massive scale,” says Harvey. “I’ve never done one this big. All the loose particles [of paint] are taken away through four filters. Nothing ever lands on the floor.” Harvey and Irwin noted some learning curves for the contractor and subcontractors, bearing in mind that this is the first building in New Zealand to be constructed to the Industrial Five Star rating. The performance of the concrete took some getting used to.
“It’s harder to work with given the recycled content and flyash involved. It also dries differently to standard concrete as the initial set cures slower,” Irwin says. Harvey says they raised the structure and roof first, giving the concrete its own protected environment to dry in – around four to five days. Another learning curve Irwin noted has been educating the sub-contractors on waste recycling, as well as purchasing environmentally friendly and compliant products, rather than the standard products.
The initial build went together like Meccano Harvey says, and the use of 3D CAD models at the shop drawing stage ensured accuracy and precision. “For us as builders the main challenge is the amount of services in this building.” For the NZDF the project marks a turning point for future building developments. “All new NZDF building design commissions require the designers to observe ESD principles to an extent that is appropriate to the building’s proposed use,” says Wing Commander Neilson.
As a plane roared overhead Harvey noted that people wouldn’t hear a thing from inside the completed buildings. “This is ten times the facility they have at present. It will be amazing.”