Royal Society impressed with PRESSS
This project’s main challenge was taking in an old building, extending it and incorporating the latest in seismic design technologies.
If a major earthquake struck Wellington, the new Royal Society of New Zealand’s (RSNZ) head office, Science House, would shake but thanks to PRESSS technology, it would be left significantly undamaged.
That’s according to Alistair Cattanach, of Dunning Thornton, who designed the structure of the new building using the pre-cast seismic structural system (PRESSS) and other damage avoidance design techniques.
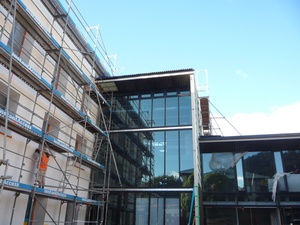
He finds a desktop toy giraffe with elasticised legs, a handy aid in demonstrating how the building will spring upright after a large seismic event. “PRESSS reduces the acceleration of the contents, reduces damage to the structure but the building still rocks, so potentially you’ve still got façade repairs to do,” says Alistair.
During small earthquakes the stiffness of PRESSS reduces movements. In large earthquakes the building becomes flexible. Ductile joints yield to the seismic forces, while individually un-bonded post-tensioned cables allow the building to rock back and forth, eventually returning to its upright position. After a large earthquake damage to the structure is limited and people can quickly resume work.
The RSNZ needed a new headquarters says RSNZ CEO, Dr Di McCarthy. An increased staff of 41 was spread over different locations; conference and lecture facilities were inadequate and the existing Science House was unsuitable for resisting seismic loads. Established in 1867 to advance and promote science, technology, and more recently, the humanities in New Zealand, the RSNZ chose what project manager Ian Mills says is “cutting edge” seismic design to build into the 21st century.
Architects Studio Pacific (architect Simon Hardy), engineers Dunning Thornton (structure) and Beca (services) designed the new building and Fletcher Construction started the project in June 2011 on Halswell Street, Thorndon.
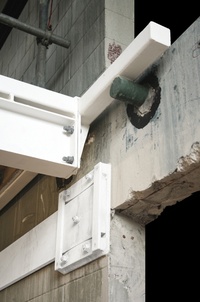
“After we got well into the design phase the Christchurch earthquakes came and Dunning Thornton were heavily involved,” says Ian. “They have incorporated all the latest findings from the Christchurch earthquakes into the design.”
Following the earthquakes the seismic designs for the building were peer reviewed, a necessary exercise, which, along with ground testing, delayed some aspects of construction. The architectural and engineering designs of this ‘super-assemblage’ are innovative and complex; timing and sequencing of construction has been atypical. The geometry of the large south facing corner window is another unusual feature and required specialised installation.
Ian says the project’s main challenge was in, “taking an old building, extending it and incorporating the latest design philosophies”. Science House, which will house administrative staff, has been stripped back to reusable bones and a third storey added. A new two-storey annexe will provide a staff hub, conference facilities and meeting rooms.
The existing building, built in the 1960s, was a stiff, reinforced concrete and concrete block structure. Mike Morgan, Fletcher Construction project manager says during the peer review, they split up the work into PRESSS and non-PRESSS areas. To reduce stiffness and increase movement and energy absorbing capacity they made vertical saw cuts in the concrete blocks up to the second floor and reconnected them with horizontal steel plates.
Around the base of the concrete blocks a 30mm cut was packed with 20mm rubber packer. Every second row of floor beams was stiffened in three places with carbon-fibre resin compound. Bolted steel work on the outside will hold the building in an earthquake. Exterior cladding is Sto-Firm that incorporates polystyrene insulation.
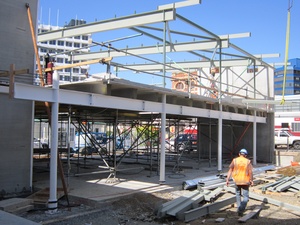
“Because of the seismic design there is a lot more detail to consider – control joints, details around windows, all additional fine-tuning,” Mike says. The back wall of the existing Science House is a PRESSS design; the front is connected to and supported by the new annexe, which comprises eight PRESSS panels. An atrium entranceway links the old and new structures.
“We have strengthened the original building and tied it to the new annexe via a big ‘truck and trailer’ connection and done a lot of checks to make sure it [the trailer] never comes off,” Alistair says. Mike points out the 200mm x 20m steel plates that will help support the building in an earthquake. His hands go back and forth. In fact during the visit you get used to the idea of rocking in a controlled sort of way.
The new generation of seismic design techniques will improve earthquake resilience, but construction is far from the traditional – excavate, lay the foundations, up with the structure and close it all in as quickly as possible.
Land under the annexe site was found to be alluvial and uneven. After excavation and unforeseen geotechnical tests were completed Fletcher began piling and preparing the foundations of the annexe. Piles are ground anchors, 10 to 12m, 200mm in diameter, and the foundations are heavily reinforced.
“There was more detail and complexity in the foundation stage – setting up the anchors and stressing area under the ducts. We backfilled the foundations, except adjacent to where the pre-cast panels were going, because we had to allow access later to the bottom of the beams to complete the stressing exercise. We weren’t able to complete all the floor slab.”
Once the ground floor slab was poured in December 2011 steel posts and beams set into the foundations went up to support the level one floor, which will ‘float’ in a large earthquake. It’s been complicated says Mike. “We had to pour the first floor slab before we could look at the tensioning exercise and the pre-cast panels. The slab had numerous large metal anchors to the pre-cast panels.”
Eight, seven-metre high, 10 to 12 tonne pre-cast panels went up two-by-two over a week, and were extensively propped from different directions prior to post-tensioning. Two 70mm diameter ducts inside each panel were threaded with nine 12mm diameter, eight to 10-metre long cables. “During that time we had to confirm that the corbels were up to strength [where the cables are anchored at the top of the ducts]. It was all a matter of timing.”
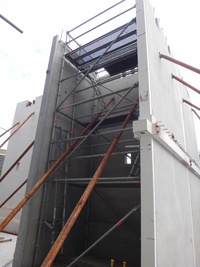
Once the cables were tensioned and wedged, cement grout was pumped up the ducts to harden and corrosion-protect the cables. Then the roof could go on. Alistair says that where the building rocks on the foundation, a steel shoe stops the concrete from wanting to burst by confining it. “That makes it a lot stronger and it doesn’t want to crack.” Steel bars installed between the panels and foundations stretch and compress as the walls rock, allowing additional energy absorption.
The wall panels are connected to the floor by large steel spigots, which allow the panels to move around without tearing the floor apart. A north-facing curtain wall is double-glazed with large, heavy windows (approximately 2.3m x 2m) and the rest of the annexe is clad in dark, stained cedar weatherboards. The existing and new buildings have contrasting finishes and textures; dark and light exterior finishes also reflect the Society’s black and white logo. The innovative engineering has influenced the design, which exposes the structural steel and raw concrete finishes to the PRESSS shear walls, says architect Simon Hardy.
“This approach puts pressure on the finished steel welds, scale of pin joints and sliding joints to be well detailed, scaled and set out,” says Simon. “The assembly of components can be challenging as the finished product is critical and influences the already complex sequencing of work.”
From a designer’s point of view Alistair says they could work on improving the building methodology. “We’ll know what to do next time,” Mike says.
By 7 August Thorndon will have a new Science House in an area where embassies, large historic houses, cathedrals, corporations and government departments are just a glance away. “We want to create a campus style environment, reflective of what the Royal Society stands for and what it tries to achieve for New Zealanders,” says Di.
“To create something respectful of the environment around it, and also meets our needs moving forward.”