The Living House – Summer 2020 edition
Rochelle Payne and her family are taking on the mammoth task of building a home that meets three of the highest sustainability rating standards: Homestar, Passive House (also called Passivhaus) and the Living Building Challenge. Completing a project that is energy efficient, uses sustainable products and is carbon-neutral has been met with many challenges. Here, Rochelle updates us on the progress with The Living House since February of last year.
Find out more about each of the sustainability ratings in the introduction to the Living House blog here. Then, catch up on part two, part three, part four, part five and part six.
Last year started off well, with lots of things happening on site. The footings for the main house were poured with concrete and the site turned into a bit of a steel jungle again. Nexans Enviro cable (PVC free and Red List compliant) turned up on site and started coming through the walls. Some earth walls were put in followed closely by our beautiful copper pipes from Kembla (honestly why would you use anything else) and even more exciting our copper rain chain arrived from the US! And with the help of Vertical Gardens we moved our green wall into the tiny house.
Then wow, did the month turn to custard:
- The tilers we had lined up to finish the bathroom couldn’t come and membrane as our shower drain is direct on XPS rather than concrete and therefore has 10mm of movement. So, no bathroom for us.
- We had no water pump, no power connection, no light fittings, no power points
- We couldn’t find a red list free comms cable, so no internet when we move in
- We didn’t have a kitchen to move in with either as the joiner was on holiday
- We still didn’t have any windows as the timber arrived late
- We also still couldn’t finish the roof as we still haven’t gotten the building consent amendment approved. Auckland Council keeps asking questions that have to go to Europe to be answered.
- Our pool was leaking and has lost 5cm of water overnight
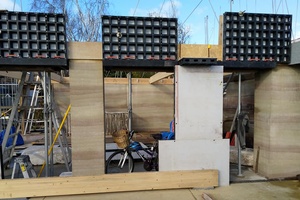
We moved into the ‘tiny house” later than anticipated, and had all sorts of things go wrong or not happen for us. We only had temporary windows in the house as the permanent windows hadn’t been manufactured due to delays in components from overseas. We had no hot water as we hadn’t found a compliant cylinder. We had no lights, no kitchen, no shower……the list just goes on and on! One of the more exciting things, however, was the first use of the composting toilet, the Waterless Composting Toilets NZ Bambooloo toilet: and, no, it doesn’t smell.
March 2019 was the month of trying to get things sorted. One of the big things that needed to be completed was the roof. We finally got the final layers of the roof on, which was very exciting as it meant that we wouldn’t get ‘wet’ anymore inside.
On the inside of the tiny house nothing was finished. The ceilings need to be painted with the Natural Paint Company paints, tethers needed to be installed, kitchens needed to be installed, showers, hot water, power points, lights, windows: What a disaster!
We did move out briefly so the floors could be polished, however it did not go to plan. The poor man thought he was going to have the easiest job ever, but it isn’t a concrete floor, it is an earth floor. So, it didn’t perform the same as concrete. And, boy, did he have trouble. There was a point in time there where they were about to walk off the job and not complete it. We told them to just do the best that they could. It looks pretty nice in the end, so we can heartily recommend them.
Pretty much nothing happened on site over the winter at all. Joel managed to get the walls to the garage up and a ring beam in, but the HYNE beams were a disaster. When they were delivered to site they were covered with mould. It was heartbreaking. They hadn’t been stored properly in the yard at Placemakers and they were ruined. So we had to send them back and ask for replacements.
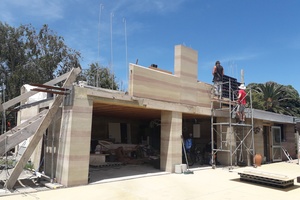
By October, when the weather started to get warmer, we actually started work on the main house! It was quite exciting. Above the garage is planned to be the master bedroom, office and ensuite. It is almost like we might possibly have somewhere to live sometime in the future.
We also managed to finish the bottle fence, although there has been an artistic difference of opinion about the final colour. Joel believes that the pure white lime is perfect whereas Chelle finds it a little stark and believes that perhaps a softer cream/yellow would have been the way to go. The dog doesn’t care either way.
We spent a lot of time installing services. We finally got a hot water cylinder installed. Thanks to the magic team at Rinnai (who documented Red List compliance for us), we were finally able to get something on site that would generate hot water for us. We are actually installing a solar hot water system (from Apricus) but we have to wait for the roof to go on the main house before we can install the racking and solar panels for that system. At least we got some hot water in the meantime, just in time for winter to finish.
The other service that we spent a fair bit of time installing was the Zehnder mechanical heat recovery ventilation system and it’s spaghetti-system of ducting! The joy of the Zehnder is that on high allergen or super cold days we can close all the doors and windows and still have fresh air coming into the house. Why wouldn’t you put one into every single house?
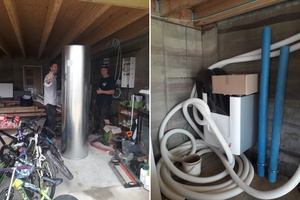
Chelle realised the answer to this at the Earth Building Association conference in November, where we were asked to give a presentation on the house. At the conference we found out that there are actually people who are quite passionately anti-Passivhaus. So much so that Chelle completely rewrote her presentation to address this issue and explain what Passivhaus is actually about as there is so much misconception out there.
After the conference, the editor of the Earth Building magazine wrote this about our talk:
“I sat up straight at our conference when one speaker spoke about Passivhaus. I think I may have been assuming that Passivhaus required you to live in a hermetically sealed box, divorced from nature and the natural environment. Instead Passivhaus was explained as a design philosophy, one that asks designers and builders to carefully consider window size, dwelling orientation etc to optimise (not maximise) solar gain. The speaker advised that the purpose of the Passivhaus standard is to create a dwelling with a low heating demand in winter that won’t overheat in summer (not always the case in passive solar).
“Yes, Passivhaus uses very exacting science to design homes to the highest possible standard, but the reason for this is that Passivhaus wants is to provide you with a warm, dry and comfortable house. Using this science allows the avoidance of draughts or leaks – too common in many houses – and ensures that any ventilation (windows, skylights etc.) is by choice. Apparently, it is not the case that a passive house has to be a hermetically sealed bubble – it should just be airtight with no unintended draughts. What I didn’t realise is that Passivhaus is actually a simplification of design, where I originally thought it was all about complicated mechanical systems. This speaker made me realise that Passivhaus and earth building could be a match made in heaven.”
We truly believe that everybody should have a Passivhaus.
Moving into 2020, our plan is to finish all the rammed earth walls and get the roof on. Anyone want to start a betting pool on how long that will take?