The Living House: November edition
Rochelle Payne writes the third blog update on the progress of The Living House. The rammed earth house in Beachlands is to be the family home of the Paynes, who have decided to target the ‘trifecta’ of sustainability rating tools: Homestar, Passive House and Living Building Challenge.
Time has moved on smartly since we last put fingers to keyboard to document what we have been doing here at the Living House. When we last updated, we were just trying to get the waterproofing of the basement slab done so we could pour the basement slab and start doing some blockwork.
I am pleased to report that the basement waterproofing has been completed and not only is the slab poured but all the blockwork for the basement walls is in place, with the wonderful Autex insulation between the double-skinned blockwork walls! However, this is also where we hit our next hitch: the basement roof.
We have a set of building consent-approved drawings that call for the use of either Tray Dec or Dimond Flatdeck, both great construction systems that would allow us to easily pour the basement roof… except for the fact that these products are manufactured from galvanised steel, which has a protective coating added to it that uses Chromium V – which is on the Red List for the Living Building Challenge!
It is possible to manufacture the steel that the Tray Dec and Dimond use to form the products without that protective coating – they just apply an oil instead – however this oil doesn’t protect the product as well during storage, and if it gets wet it would form a type of white coating (a type of oxidation). Apparently it doesn’t affect it structurally, but it doesn’t look very nice.
We could still get this product, except for the fact that the steel mill will only take a minimum order of 4 ton, which is about 400 times the amount that we require for the Living House. And we can’t really ask either Dimond or Tray Dec to place this minimum order for us, as they would then end up storing a lot of extra product that doesn’t store as well since it doesn’t have the normal protective coating on it.
Therefore, as we now cannot use Tray Dec or Dimond Flatdeck for the roof of the basement, for the last two months we’ve been scrambling around trying to find a cost-viable alternative! The options that were on the table were:
- Rib and timber infill (structural engineers first choice)
- Formwork and a solid slab (not pretty to put the formwork up on site!)
- Precast.
Somewhat surprisingly, we have actually ended up going down a completely different route and have opted for a suspended timber floor to the basement (which is also the floor of the garage). We have done this for a large number of reasons but probably the main two are:
- To reduce the amount of concrete that use in the Living House. We have nothing against concrete and we think it is a beautiful material that plays a vital part in the construction industry. However, apparently the world is starting to run out of sand and we want to be good global citizens and play our part by only using resources that we have to use.
- Construction detailing. As we are building the Living House ourselves, and since building is not actually our trade, we were concerned about how we were going to manage the more complicated detailing and formwork that we would have had to use with all of the concrete options. The timber detailing is far more straightforward and we feel like we will be able to manage it ourselves on site.
The good news is that we have just placed an order for HYNEBeams from our wonderful IBuilt supporters as well as some 135 x 45mm topping timber from our other wonderful supporters Abodo.
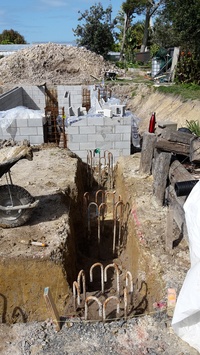
I mention these two suppliers because being Red List compliant is very important to us, and both of these companies can provide Red List-compliant timber products – there are not many companies out there that can do this! Most get tripped up at the timber treatment step, tending to use the common CCA (chromated copper arsenate) timber treatment. Arsenic is on the Red List, so that is a no-go for us.
In other news, we have also started to dig out the strip footings for the one-bedroom MHU (minor household unit), which is the first part of the Living House that we will be constructing. This part is actually very important to us as we intent on moving into it and living on site while we are building the main part of the house.
However, with all of the piling problems and the wet, wet winter, we are somewhat delayed and are only now starting work on this, which doesn’t bode well as we need to be out of our rental by the end of January!
We are digging these footings by hand, and when I say we, I mean it’s mainly me digging these footings by hand. Everyone who finds this out looks at me like I am crazy and asks why we aren’t using a digger. Firstly, it’s really hard to get hold of contractors these days. Everyone is so busy that I rather struggled to get our favourite digger driver to come and do the work.
I am also finding it really satisfying to be physically building the footings myself. It gives me time to think through what needs to happen on site and the ordering of works, and I’m actually finding myself solving a large number of problems before they occur while I dig.
I would never call myself an eco-warrior (although many of you may disagree based on the design of our house!). I tend to view myself as pretty mainstream – however one area where I think the ‘hippies’ have it right is that we all need to slow down a bit and get more involved with our own lives.
It is such a shame that the majority of us tend to outsource so many things that are actually really satisfying to do yourself. It is pretty easy to wield a spade, and it is downright simple to build using earth – everyone could be involved in building their own homes. I’m hopeful that we might manage to inspire some other people to give it a go themselves.
Wrapping up, the aim is to have the following done by Christmas: firstly, the suspended timber basement roof on. Secondly, the hole around the basement backfilled (i.e the big pile of dirt gone!). And lastly, the MHU strip footings poured with concrete and ready for wall ramming to start in the new year. Let’s see how it all goes…
Read the introduction to the Living House here, and the second update here.