The makers of Venice
Future Islands is this year’s Venice Architecture Biennale project – it sounds good saying “this year’s”, doesn’t it? The implication is that New Zealand’s presence on the ‘world stage’ (as we always say) will become of more regular and less of an infrequent shot at fame at what has been called “the Olympics of world architecture”.
For me, this will mean the ability to explore aspects of architecture as other countries do and less of the fraught occasion when we attempt to summarise and present the whole history of New Zealand in one go. As Future Islands co-leader Charles Walker says, this year’s project is more “speculative and forward-thinking; to project alternative ways of living”.
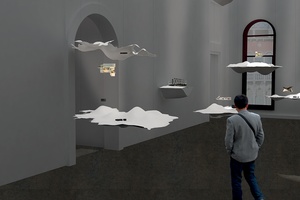
Anyway, this article isn’t so much about the Future Islands concept and content — that’s for them to show (and us to debate) in future months — but to do with the technology behind the project. And that’s a change as well: past Biennale projects (and they have been terrific) have also focused on the technology of the past — sticks and stones — but this one will explore a new 21st-century technology: composite construction.
The actual floating islands in the Venice pavillion are being built from composite and the stuff isn’t just for scale models, of course: aircraft and boats are built out of it and now buildings are using this technology.
Core Builders Composites relocated here from Seattle as a spin-off from the America’s Cup yacht-racing series and are based in Warkworth; this was not for any proximity to the coast but because that’s where they found an appropriate building. As a subsidary of Oracle, their focus is on building racing yachts but as a stand-alone firm they seek other work also. They see themselves as prototypers rather than mass producers; so, that is ideal for architectural work from models to moulds to actual buildings, such as the roof of Cheshire Architects’ interpretation centre at the Marsden Cross Historic Reserve in Northland, which they built last year (more on that later).
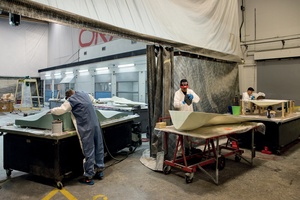
What are composites? Basically, objects that have a skin of fibreglass or carbon fibre over a foam or honeycomb core. More three-dimensional objects tend to have polyestyrene or PET (polyester) cores, while panels have a very light but strong honeycomb core. The skin selection for objects is based on the strength and finish required.
Initially, the Future Islands’ team considered options such as 3D printing the islands (using milk powder!) or infusing a felt or flax mixture – and those materials would have added quite a resonance to the project. However, they finally settled on composites because Future Islands’ team member Jessica Barter, of Bureaux, had looked at the technology for the roof of a house.
The floating islands in the exhibition have either foam cores, milled with a CNC router (although the factory can robotically slice foam also, using a hot wire), or PET at their hearts. Most have an e-glass skin (that’s a type of fibreglass and not to be confused with the low e-glass we put in buildings), and then a sprayed paint finish using a Resene product to achieve the desired white colour. Some of the thinner islands are even made of infused hemp!
A bigger island works also as a seat for exhibition visitors and has a carbon-fibre skin for added strength, which is recycled from Boeing 787s. The end result is that all the islands are extremely light for transporting, as well as being resilient. A number of adjustable brackets have been developed to fit the slatted ceiling of the Venice pavillion and each island has been drilled and fitted with small caps for the suspension wires. The exhibition will contain a number of models and be bathed in images from projectors, although that’s an aspect of the exhibition to be discussed at another time.
So much for scale models, but what are the architectural applications? As I tell our students at The University of Auckland, the digital tools and techniques, CNC routers and 3D printers they are using today to build their models are the same that we will be using in the future to build full-scale buildings.
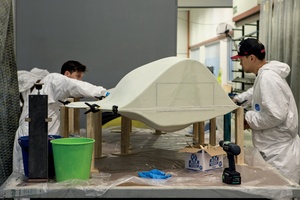
Core Builders mostly build yachts and boat appendages and so on, and composites are already used in aircraft; so, plainly, the material works well in high-performance areas but buildings have other challenges. Core Builders (and similar outfits) produce two categories of objects: moulds (or tools, as they call them) and the actual finished product. A spiral staircase in a house by Stevens Lawson Architects is an example of moulds created for a concrete pour.
The roof of Rore Kahu, the Marsden Cross Historic Reserve interpretation centre by Cheshire Architects, is a full-scale object created by Core Builders. The future SkyPath, which will hopefully clip onto the north side of Auckland’s Harbour Bridge, providing a pedestrian and cycle path, is a good example of how composite technology will suit a job where strength and light weight are crucial to the structure.
The process starts with the production of drawings in the factory. Even Revit drawings have to be redrawn as the manufacturing process works to .2 of a millimetre, an order of magnitude different from a couple of mil here or there, which we tolerate in construction. And given that most architecture starts as a 6B pencil smudge, that’s a precision which we need to get used to in a digital manufacturing world that can’t fudge details.
The digital model is fed into automated machinery for the manufacture of the cores but skins are generally laid on by hand, although moulds can be used to ensure greater accuracy. The biggest object they can construct is 18m x 6m x 3m, which is definitely of architectural scale. But Rore Kahu, for instance, was built in two halves in order to be trucked to Northland. They set up a jig on site and bonded the two halves together and then the roof was lifted into place as one whole unit.
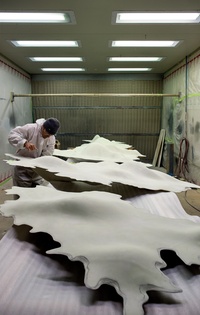
The cost of the process is not as high as you would think as the materials are not wildly expensive and are improving constantly; you are paying for machine time and labour and there can be a fair amount of thinking time involved as well. Obviously, composite structures are strong and their light weight reduces foundation costs. Holding them down is the main issue as the things generally want to fly or speed off like their cousins, aeroplanes and yachts. Unlike metal, there is no expansion or contraction but flexing and stressing may be a concern.
And, of course, while there is no rusting or corrosion or worries about dissimilar metals, exposure to ultraviolet radiation, weathering and durability will be key issues to consider. Like many materials these days, it’s a decent paint coating and maintenance that will be important and Rore Kahu has a two-pot Resene product finish. Buildings can be altered as they age too; however, just as Rore Kahu’s two halves were bonded on site, composite products can be drilled, sawed and re-bonded on site at a later date.
I’m looking forward to Future Islands, and this time around it seems the Venice Biennale project, apart from its speculative content, may in several ways be a look of the shape of things to come.
CASE STUDIES
Rore Kahu
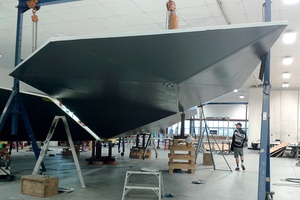
Rore Kahu, the Marsden Cross Historic Reserve interpretation centre by Cheshire Architects, has a roof that is a composite product made from panels with PET cores and e-glass skins, cut on a five-axis machine then bonded together; there is no structural steel inside the roof assembly.
The roof was trucked from Core Builders Composites’ Warkworth factory to the Northland site in two halves, bonded together on the ground (using a jig to ensure accuracy) and then lifted into place as a whole. The roof was built with holes for bolting flanges to the steel posts that had been cast into place previously. It fitted precisely – except for one post that had to be adjusted with a site weld. Sockets were built into the roof with carbon-fibre lining to accommodate downpipes installed after the lift.
It is fitting that a building celebrating 200 years of Christian presence in New Zealand uses technology that spans the centuries: while the roof is very 21st century, the walls are rammed earth, similar to the 1842 Pompallier Mission, also in the Bay of Islands.
Spiral Staircase
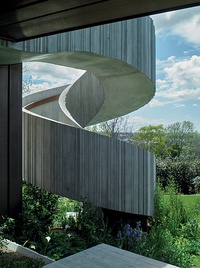
A house by Stevens Lawson Architects sports an exterior helical staircase that was cast from concrete in one record-breaking pour by Bannan Construction. The moulds and plug components for the staircase were fabricated by Core Builders Composites and produced to a very high standard of accuracy – within .2mm. But the main issue in a concrete pour of this height is the enormous pressure on the whole structure as there is potential for the formwork to explode.
The composite moulds (or tools, in the jargon of the manufacturer) were strong enough to stand up to the forces involved. Timber was added for a textured finish. Could the stairs have actually been built out of composite too? Apparently yes, and this would also have achieved an appropriate finish so that the steps wouldn’t be slippery. The additional advantage of this kind of prefabrication element, of course, is that you can build in factory conditions without exposure to weather.