Transforming timber
We look at an innovative New Zealand-made timber pavilion, slated to appear at the 17th Venice Architecture Biennale in Italy.
How do you make wood that carries load go around a corner? This is an increasingly urgent research question answered by a New Zealand-made timber pavilion that will soon be on show at this year’s 17th Venice Architecture Biennale, running from 29 August to 29 November. The exhibit is a collaboration by staff members Andrew Barrie, Mike Davis, Kathy Waghorn and Paola Boarin at the University of Auckland School of Architecture and Planning. The theme underpinned by the project is related to the innovative use of timber as a building material capable of producing high quality architecture, especially in terms of carbon sequestration and earthquake resistance.
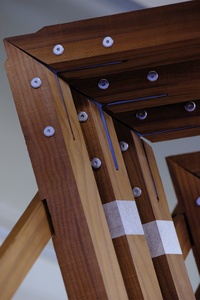
The work – Learning from Trees: Transforming timber culture in Aotearoa – is both elegantly simple and outrageously complex. It comprises 436 thin sticks of Abodo Vulcan pine notched and screwed together in two criss-crossing diagonal wall and roof planes, forming an airy 35sqm wedge-shaped, 3.3m-high pavilion. The sticks of the lattice wall planes join the sticks of the roof lattice via carefully cut mitre joints each fixed together with a small internal steel corner bracket and a couple of barrel bolts. Leading the structural side of the endeavour is Andrew Barrie, whose research involves the advancement of timber technology both in his teaching and his professional practice.
Barrie describes the structural concept of making timber go around a corner as being like the outer crust of a sliced loaf of bread – except that the slices are cut on a 60-degree angle. Here’s where the complexity begins to show in the band-saw-cut, diamond-shaped profiles of each stick and the drop-saw-cut angles of the mitre joins at each end. “We have shapes that are tricky but the corners are simple,” says Barrie, noting that it’s the two layers of timber screwed together in lap joints that make the structure stiff.
The pavilion is built using extensive digital modelling – the notches for the laps cut, and all the screw holes drilled, using the School’s CNC flatbed milling machine and an elaborate jig. The result is a slender, lightweight, sustainable structure pointing the way for a different kind of construction with mass customisation potential. Plus, it’s using highly sustainable pine, treated to behave like a hardwood.
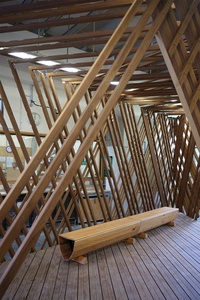
Crossing through the project is a long seating bench made from digitally tooled kauri timber, salvaged from a former Housing New Zealand house. The theme of reuse builds on the research of Mike Davis and his use of digital tools in a timber craft tradition. Here, the kauri seating benches have been made tactile by milling the ripple patterns from a photograph of low-tide sand at a local beach into the kauri surface.
“This stuff is like treasure to me,” says Davis. “If you pull something down, you look after that material; you don’t chuck it in the dump.” After the lead paint was stripped from 100 linear metres of weatherboard, the reuse yield was about 45 per cent. “I work away on this stuff and I like the way it changes.”
The structure is now disassembled, packed in a container and on its way to Venice, where this new take on the New Zealand building tradition of ‘joining sticks together’ will be received on an Italian stage.
Other staff members and students involved in the project are: Max Smitheram, Denice Belsten, Melanie Milicich, Robyn Chin, Mark Andresen, Dylan Waddell, Bronte Perry, Josh Crandall, Will Challombe King, Scott Facer, Vincent Lardeux and Sharon Fitness.
Editor’s note: This article was accurate at the time of publishing in Architecture New Zealand magazine (March 2020); however, due to the ongoing global COVID-19 pandemic, details surrounding New Zealand’s participation in the 17th Venice Architecture Biennale are subject to change.