White gold
Outside of the global dairy industry, the name Yashili probably doesn’t ring too many bells. However, all that is about to change as the Chinese infant milk formula giant invests NZ$200 million in a dedicated processing plant at Pokeno, situated at the bottom of the Bombay Hills, south of Auckland.
“Yashili is one of the leading producers of infant milk formula for the domestic market in China and is regularly named among the top 500 most valuable brands in China. The infant milk formula processing plant at Pokeno marks the company’s first major offshore investment,” says Yashili New Zealand managing director William Zhao.
“China’s infant formula market is expected to grow to NZ$32 billion by 2017. The challenge for Yashili and other manufacturers is to keep pace with demand while maintaining a high level of quality control. That’s why we have looked to New Zealand and its internationally recognised expertise in the manufacture of quality milk powder. In fact, Yashili has used New Zealand milk powder exclusively in our infant milk formula since August 2010.”
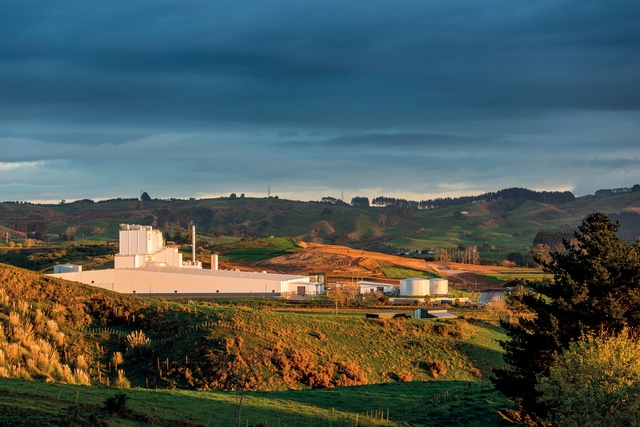
Construction firm Ebert Construction – which has built a reputation as a specialist in the design and construction of dairy plants having worked with Synlait, Miraka, Tetra Pak and Fonterra – was brought on board to work alongside GEA, the project’s process contractor, to deliver the plant.
“The key components of the job for us are the dryer building, which is 36 metres tall and includes: an integrated evaporator hall and stair/lift shaft; a two-bay tanker reception; silo slabs; ingredients area; a packing and palletising area; chemical storage bund; and a 20,000m2 store,” says Ebert Construction project manager Sathy Thurairajah.
Working alongside GEA and also with Babbage Consultants, who were project managers for Yashili, as well as having a client primarily based offshore, must have added greatly to what was already a challenging project?
“Yashili has a good team in New Zealand – the operations manager, services manager and plant manager all had had a lot of local exposure, so that helps considerably. The only challenges were down to Yashili being a new client – as opposed to Fonterra for example, which already has a lot of systems in place.
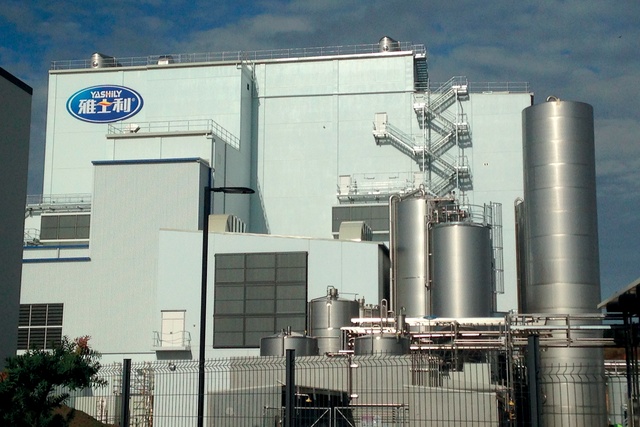
So there were a number of unknowns that necessitated significant involvement at the design phase and a few changes while construction was in process; but there was always an open line of communication that meant any issues were dealt with swiftly and didn’t stall proceedings,” says Thurairajah.
“The greatest contributing factor impacting the project – as with any construction project in New Zealand – was the weather. The weather on the other side of the Bombay Hills is a very different beast to that on the Auckland side, often in complete contrast; so, yes, the weather played a huge part during the 18-plus months that we were on site. It also was one of the determining factors in the design of the plant, given that the height of the drying tower required earthing rods to be integrated into the tower’s structural steel.”
As well as taking the weather into account and designing to the latest seismic regulations, Thurairajah says there were a number of other considerations that meant this project was at another level to the dairy and food processing plants they usually design and build.
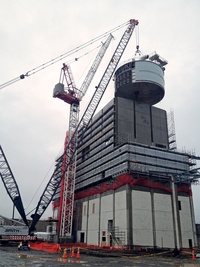
“Inside the tower there is a huge amount of structural steel elements – staircases and platforms – which made for a tricky construction programme. These had to be installed in parallel with GEA, who was in charge of the processing plant. Processing elements would progress to a certain level and then we could install the stairs and platform elements. This required a daily co-ordination meeting with GEA to make sure both streams were on the same page and that there were no clashes.”
The logistical demands of the physical construction were compounded by the strict hygiene level required for the production of infant milk formula, making the project one of the most complex builds to be involved in, says Thurairajah.
“The imperative to meet hygiene standards pervaded every aspect of the project, from ensuring the dry store was insect proof through to using stainless-steel electrical conduits and pre-cast concrete columns, wall panels and stitch joints. Even the surface treatments – flooring and wall and ceiling paint – are hygiene rated and pinhole free, all of it requiring that extra level of vigilance. Eberts always aims to innovate from project to project. On this project, the building finishes are at another level. In fact, the quality of the finishes had to be signed off by various parties including AsureQuality before Yashili could obtain the requisite export licenses.”
Such was the nature of the build that, unsurprisingly, the project garnered the attention of a number of other interested parties. “Given the physical challenges associated with the height of the structure and the complexity of the build, health and safety was of paramount importance on this project,” says Thurairajah. “Not just for Ebert, GEA, Babbage and Yashili, but for a number of external parties including WorkSafe NZ, which used the job as one of its pilot projects while transitioning into the new entity.
“I’m proud to say that one of the successes of the project was that there were no lost-time injuries or fatalities during the construction phase.” Handover of the plant to Yashili New Zealand Dairy has been completed and now the company waits for the widely publicised overhaul of China’s food safety laws to fully come into effect before it ramps up production.
“Once fully operational, the plant will employ 130 full-time staff and be able to produce up to 8.4 tonnes of formula an hour, or 52,000 tonnes per year, to supply the increasingly demanding Chinese market,” says Zhao.