Eco-Bank - ASB’s new HQ
ASB’s new headquarters is being built in the Wynyard Quarter in Auckland’s CBD. It’s a complex build, incorporating unique design features and the latest in energy-saving technologies. And it looks pretty good too.
I like the Wynyard Quarter. It looks great and the bars, cafes, funky outdoor spaces, trams and restaurants makes it a fun place to visit, day or night.
So it was with some surprise that I found myself – on a lovely summer afternoon at the end of February – visiting what will soon become the new corporate headquarters for ASB Bank. At first glance it seemed a strange part of town for a corporate office to move to, but looking around, I can see why they chose it.
Work is well underway on the 21,000sq m building, which is situated on a 6495sq m site on the corner of Jellicoe and Halsey Streets. Main contractor is Fletcher Construction and the project director for Fletchers is Alan Gray. ASB – who will be the anchor tenant – have taken out an 18-year lease for 19,500sq m of the six storey building. Level two will have 97 car parks and the ground floor will have 1500sq m of retail space.
There are two distinctly different buildings which will be connected by fully-glazed, multi-level walkways. Highly technical in terms of how it operates, each floor layout throughout the structure will be different. The main entrance is in the corner building fronting Jellicoe and Halsey Streets [building 23], which has an interesting curved façade with vertical fins. In contrast, the other building [building 22], is square in stature and will be covered in 5000 individual aluminium louvres. Arranged in a pattern of leaves, they are positioned in front of the northern façades to deflect heat and light without obstructing the harbour view.
Designed to mimic Auckland’s volcanic landscape, the distinctive funnel on top of the building is designed to create a natural air flow in the building, by utilising a fresh air displacement system and drawing natural ventilation through the building’s windows and so minimising the need for mechanical air conditioning. Based on the ‘Venturi effect’, the ventilation system will utilise thermal mass and extract heat from the building and exhaust it throughout the building. Louvres in the funnel on top will open depending on wind direction, effectively ‘dragging’ heat load from the building. This passive type of ventilation will be controlled by an internal computer system.
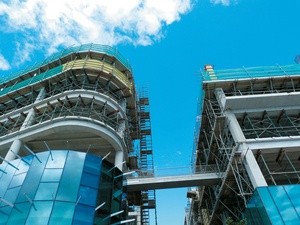
Site manager Tonchi Glamuzina says originally the funnel was going to be an aluminum-clad timber framed structure, but after putting the concept through a ‘buildability’ and design process, it’s now a fibreglass composite shell, which is being manufactured off site at Yachting Developments in Hobsonville. It will be transported to the site in one piece. Because of its size, it will be delivered by barge. “It’s huge,” says Simon Ayris, site engineer. “Massive.”
The design for the funnel has changed quite a bit as the project has developed and the designers and consultants have had to work closely together to find the right solution. “There’s a lot of planning going in to how the funnel will be installed and how it will work,” says Tonchi. “It’s been working quite well in terms of how everyone is working together.”
“Everything’s been 3D modelled,” says Simon. “There’s no way you could do this any other way.”
On the top of building 22, skylights will draw natural light into the atrium. ‘Intelligent’ light and occupancy sensors will allow for lights to be turned on and off as people enter or leave or reduce artificial lighting when natural light illuminates office spaces. The façade will also provide solar and wind control, allowing large amounts of daylight on to the office floors and windows can be opened on all six levels as well as in the central atrium, to provide natural ventilation throughout the building.
This is a complex build, which has put enormous pressure on the consultants and the project managers but despite the challenges it is clear that things are moving along well. Looking at the plans, it is obvious there are some interesting aspects to this build and the guys are more than happy to discuss them.
“We have a mixture of precast concrete, structural steel and in situ post tension beams, which is a bit different from most projects around Auckland at the moment,” says Tonchi. Precast concrete construction is being used on the lower levels, where normal structural columns are being used. But from level three post tension beams are being used, which are beams that are poured in situ and then tensioned later. This is done to increase the span of the beams. For this build, the middle of the building is an open plan atrium and the designers wanted to minimise the use of columns.
“Then as we go further up the structure we’ve got structural steel, which the architects have introduced into the mix,” says Tonchi. “Not only have we got post tensioned beams, we’ve got post tensioned beams which are tensioned through structural steel.”
Jeff Esquilant, site superintendent, says the beams had to be made on site. “We prefabricated the reinforcing for every one of the post tensioned beams – 36 in all – here on site and craned them into position,” says Jeff, pointing to the space where they were fabricated; the only space big enough on site which is the road running between the two buildings – Te Wero Lane.
“We built the plywood platform and marked out where all the penetrations were, to make sure everything lined up. It took a bit of planning but it worked out well.” The beams – or trees as they are called – are complex in design and Tonchi says Simon and the team spent a lot of time getting them right for site application. They are a custom design and in terms of installation pinpoint accuracy is critical. “It’s quite tricky,” says Simon. “It’s all custom cut, custom welded. Nothing’s off the shelf here.”
Simon and Jeff have worked together before on the Eden Park redevelopment and lessons learnt there have been applied to this project. Simon says the challenges on this build are similar, in regards to the steel beams. “You learn something on one job and tweak it up a little for the next one,” says Jeff.
Walking around, I’m struck by how big the project is. It’s a hive of activity and, it turns out, is currently New Zealand’s largest commercial building project. “It’s great to be involved with something different,” says Jeff. “Something with a bit of a challenge, and something out of the ordinary rather than just a box.”
As we talk, I can see the guys are really enjoying the challenges of working on the project and I say so. “I don’t think there’s another job like this one in New Zealand,” says Simon. “It’s a good job; a good location for a build,” says Jeff. “There’s a good atmosphere around the job and we’re all getting on with it.” Jeff pays tribute to the crane drivers as well. “The crane’s run the job. Without a good crane crew nothing gets done. They’ve done really, really well.”
“We’re a close-knit group,” says Tonchi. “We’ve got a very good team from the consultants right through to the subcontractors. You’d be hard-pressed to find a job of this sort of quality around.”
An interesting feature of the build is the glazed, multi-level walkway that connects the two buildings and which floats above Te Wero Lane. “The walkway and bridges are fixed to one of the buildings [building 22],” says Simon “and they slide on the other side. There’s a steel pin on the fixed end that goes through a slot on the other side.” This allows for considerable movement in an earthquake – up to 300mm for the higher levels – and significantly reduces the risk of collapse. The stairs also have extra seismic gap detail. They sit on a steel plate with a gap of 150mm, so plenty of room for movement.
The designers have gone to a lot of trouble to incorporate innovative sustainable features in the project. A rainwater harvesting system will be installed to supply potable water for irrigation and toilet facilities and will account for around 70 percent of the building’s water requirements. This is a ‘smart building’ and is managed by an integrated technology system, which ensures that lighting, access, security, communication, climate control and connectivity all link together. The façade will provide solar and wind control, allowing large amounts of daylight on to the office floors and windows can be opened on all six levels as well as in the central atrium, to provide natural ventilation throughout the building.
As we walk through the site, I notice some areas of the concrete floors are covered up. “That’s to protect the floor,” says Jeff. “We’ve got black coloured concrete underneath, which will be exposed and polished when finished.” Even though it’s only half completed, you can see that there is considerable attention to detail. Because there will be no covered-in ceilings – all the concrete will be exposed and painted – the team are taking extra care when working with the precast to ensure there’s no residue or slurry seeping through. “We put cloth between the precast to stop any of the slurry getting out,” says Jeff. “This stops leakage and saves someone spending half a day cleaning it up. Saves us a whole lot of work later on.”
Before the project even started, nine ‘dummy’ columns were made to make sure they had the right mix and consistency. “It looked a bit like Stonehenge outside the office there for a while,” laughs Simon.
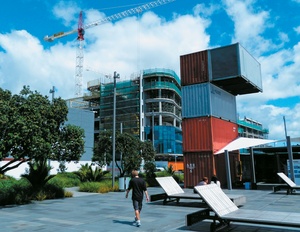
The building sits on reclaimed land – indeed the whole Wynyard quarter is on reclaimed land – and this provided its own set of unique problems. The team used a new method of piling relatively new in New Zealand called Continuous Flight Augering or CFA. Some of the piles go down 20 metres. The reclaimed land was very hard to work with, at times becoming soup like in consistency. The sub base material consistently failed to come up to strength. “The solution was to mudcrete the sub base material which proved very successful,” says Tonchi. As a result, the building is now well founded into the Waitemata sandstone bedrock.
A striking design feature of the building is that when completed, nearly everything will be exposed – from the concrete walls, stairs, ceilings, columns, beams and floors, to the pipes, service cables and even the lift shaft, which will be encased in glazed glass. The building will be see-through – inside and out – with the glass forming parts of the ceiling on some levels as well. Walking around the outside of the site, Tonchi points out the corner of building 22 which has a cantilevered slab or section on level six which pokes out of the building and overhangs the lane below. This will end up supporting a closed in glazed balcony.
“On a typical construction detail you normally have a bit of tolerance here and there. On this one here there’s very little. It has to be bang on,” says Tonchi.
Derek Shortt, ASB’s general manager property, says ASB North Wharf presents unique challenges, especially around the use of steel and concrete, as well as advanced boat building techniques. “In our experience Fletcher Construction thrives on these sorts of challenges, and we are pleased to see that thus far the project is proceeding on time and on budget.
“ASB has a long standing and successful relationship with Fletcher Construction,” says Derek. “Back in 1991 Fletchers built the award winning ASB Bank Centre in Albert Street, and over the years a strong rapport has developed between the two organisations with Fletchers being involved in a large number of the bank’s branch refurbishments.”
When the ASB move in to their new headquarters in May 2013, they will be moving to a fast growing and vibrant part of Auckland’s CBD.
If I worked there I think I would be very happy indeed.