Passive, active and simple
Ferdinand Oswald explores three research pathways to sustainable housing design and how they might fit in with the Aotearoa climate.
My wife, our two children and I came to Aotearoa New Zealand in January 2019. We quickly found a beautiful, stand-alone, rental house in Saint Heliers. It is a typical weatherboard-clad, single-glazed, timber-framed home from the 1950s. We found the interior of the house became very hot in summer and very cold in winter, except for one place: the kitchen pantry. In summer, the small pantry was cooler than the rest of the house was and, in winter, it was warmer. My family commented on how often I was disappearing into our small pantry to warm up or to cool down. The house was reconfigured in the 1990s; the original main house entrance, a solid concrete stair landing, became the supporting floor for the pantry. The reason for the thermal comfort in the pantry appears to be the following:
In summer, a broad-leafed tree shades the pantry’s concrete base from direct solar heat gain (see Fig. 1). The concrete base is passively cooled by the lower night temperatures. During the daytime heat, with the benefit of the tree’s solar shading, this stored passive cooling is released hours later into the interior of the pantry.
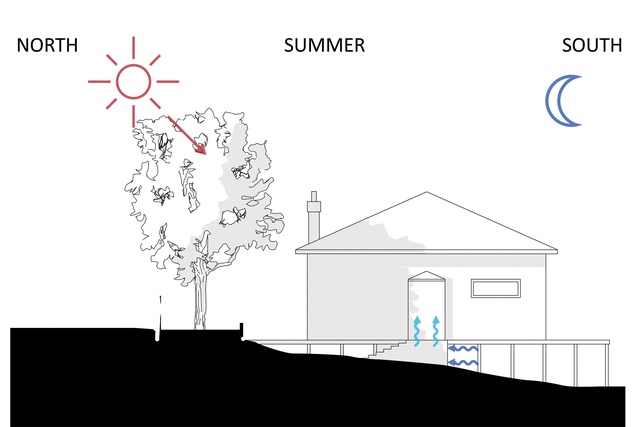
During winter, the tree loses its leaves and the sun shines directly onto the pantry’s concrete base (see Fig. 2). Heat is stored in the concrete and released into the interior at night, making it warm and comfortable. In summer and winter, the mass thermal storage of the solid concrete improves indoor comfort within the pantry, in comparison to elsewhere in the timber-framed construction. It releases its stored heat or cooling into its surroundings. You will still find me standing in that tiny but very comfortable pantry space.
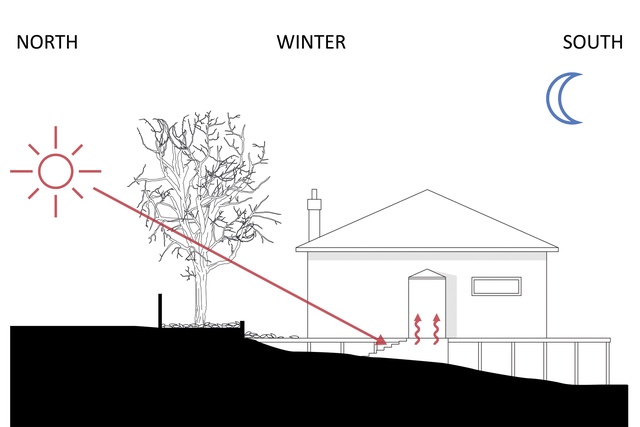
Passive House
After graduating in architecture, I worked with Stefan Forster in Frankfurt am Main, Germany, on medium-density, residential apartment buildings. In our projects, we tried to incorporate the qualities of 19th-century housing typologies from middle Europe by using solid materials like brick and larger windows sizes, such as in the example of the Westgarten project. The lively façade aesthetic incorporates clinker brick spandrels placed in horizontal bands, continuous, light-coloured spandrel cornices and distinctive rounded building corners, giving an overall sculptural aesthetic, reminiscent of the city’s 1920s’ architecture. Brick is a wonderful material – as it ages, it becomes even more beautiful.
In 2005, our new Campo building design project in Frankfurt required us to design a similar-sized development to the Westgarten project; however, it had to be designed to passive-house standards. In Germany at that time, only small-scale passive houses had previously been designed and built. We found that such a large, passively heated, residential building façade required a generous thickness of thermal insulation to keep the heat in during winter and avoid high energy demand.
We researched using a brick-veneer façade, similar to the Westgarten project, and added the volume of insulation required for a passive building. However, the façade assembly was becoming too deep. It encroached significantly into the rentable floor area, which would have lowered the client’s rental income. To achieve the client’s brief of optimising the available rental floor area, we had to design a thinner, passive-energy building façade. The outcome was an exterior insulation finishing system (EIFS).
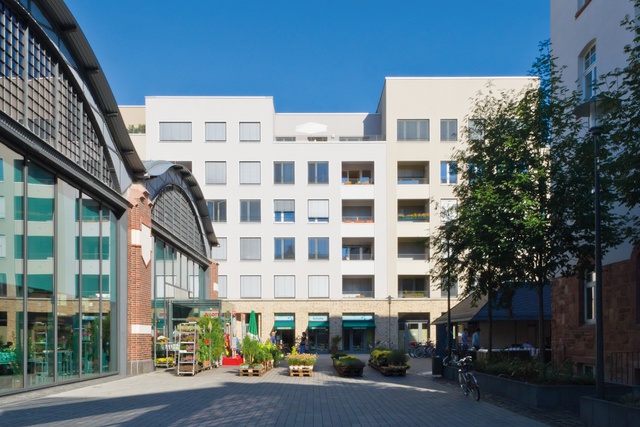
The Campo, a passive-house-standard building project, was a great success. The development, the “largest inner-city passive-house project in Germany”, won the 2011 Green Building Award of the City of Frankfurt1 and received special recognition in the Deutscher Städtebaupreis (German Urban Development Award).2 The building occupants are still very satisfied; they have perfect indoor comfort with no need to use any heating or cooling device.
However, I was not at all happy with the project. Considering the whole lifetime of the building, the building design did not consider the embodied carbon footprint of the EIFS façade system. The system is made from expanded polystyrene (EPS) and multiple layers of render, plaster and meshes, which are all glued together. The EIFS cannot be disassembled into its separate materials and component parts and, therefore, cannot be fully recycled. That means, in demolition, the façade system will become landfill waste. The passive-house strategy reduced the building’s operational carbon footprint but the embodied carbon of the building itself was not considered. I could not understand why the building’s embodied carbon was not considered by the jury of the sustainability award.
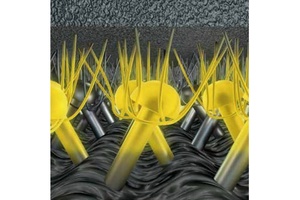
The outcome of the Campo project motivated me to focus my career on academic research, which would allow me to develop new building systems that promote sustainability and improve building industry practice. After starting as an assistant professor at Graz University of Technology, I was offered the opportunity to develop a successor to the EIFS façade system by Jochen Stotmeister, the CEO of the German company Sto (the world market leader in EIFS). I created and led the research group for the ‘facade4zeroWaste project’. We developed a fully recyclable, externally insulated façade system that can easily be dismantled after its lifespan and reused via an innovative grip fixing system consisting of mushroom-shaped heads and loops (see images at right). The idea of grip fixing instead of adhesive fixing in the façade was new to the building industry. The fact that ‘grip fixing’ was already used in nearly all sectors (automobile, aeroplane, clothes) other than the building sector guaranteed the project’s huge success.3
Over the next six years, we developed the ‘StoSystain R’ product system, relevant to architects and designers, gained the requisite patents,4 undertook certification testing and released the system in German-speaking countries.
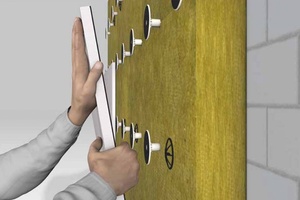
My arrival in New Zealand raised a question for me: How can we adapt specific building technologies to make them suitable for different locations in New Zealand? One of my key research areas focuses on the reduction of air conditioning use in tropical and subtropical regions.5 The key finding is that the use of air conditioning can be reduced through passive cooling methods (natural ventilation, thermal storage, etc.), architectonical means (floor plan, façade and building volume structures) and avoiding reliance on mechanical heating or cooling. This outcome was finalised in my doctoral dissertation and the publication, Reduce A/C – Reducing the utilisation of air conditioning in high-rise buildings in subtropical and tropical climate regions.
Active House
One of the supervisors of my doctoral work was Werner Sobek. He is the key person in Germany for sustainable architecture and a co-founder of the German Sustainable Building Council.6 He developed ‘Efficiency House Plus with Electromobility’ in Berlin in 2011 with his Triple Zero concept, using thin, photovoltaic film panels as façade cladding. The building produces energy for the whole house and output for electric cars. The Triple Zero concept means: 1) Zero Energy Consumed, the building requires no energy; 2) Zero Emissions, the building produces no CO2 emissions; and 3) Zero Waste, no waste is produced during building alterations or demolition. At the end of its life cycle, all building elements can be fully recycled without any components needing to be burnt or sent to a rubbish dump.
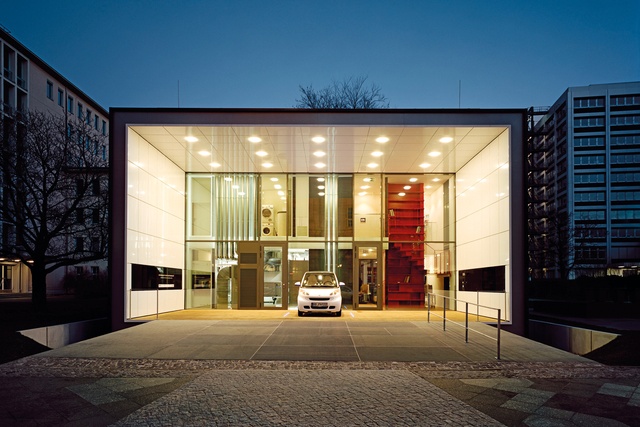
The solution here is in the detail. Nothing is glued together in the wall system. Nearly all building components are fixed together so that they can be disassembled and directly reused or recycled (biological or technical circle). But, to offer such sustainable benefits, a top standard of technical technology was necessary, such as “a high level of building automation and installation of a comprehensive building service”.7
Build Simply
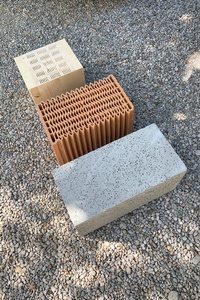
The research houses in Bad Aibling, Germany, focus on the results of the Build Simply research group at the Technical University of Munich, led by Prof. Florian Nagler. The Build Simply strategy reduces the operational carbon and embodied carbon of a building. According to Prof. Nagler:
“With the help of several thousand different room simulation models, it was investigated what a simple house should look like that requires little energy in winter and does not overheat in summer. The robust optimum was sought, i.e. a variant that works well, regardless of the actions of the users. By reducing the buildings to the essential and necessary, it is possible to create long-lasting and environmentally friendly houses – as a counterpoint to the current trend towards ever-more-complex, short-lived buildings.”8
In 2020, three demonstration buildings were built in Bad Aibling. Each used a different building material: porous concrete, vertically perforated brick and solid timber with air cavities. All material systems are capable of performing as load-bearing structures and have the benefit of high thermal insulation performance.
The Build Simply strategy pursues a number of goals in building construction, which include: robust building technology; long-lasting, durable surfaces; climatically inert building components as a result of thermal storage mass; low operating costs thanks to reduced building complexity; separation of building services systems and building structure; and exploiting the benefits of prefabrication.
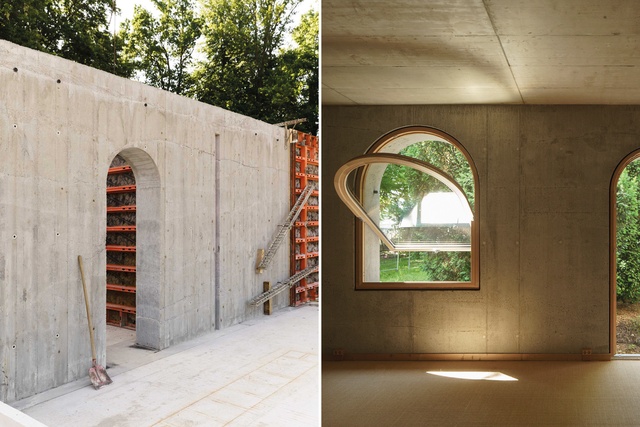
The number of component layers in the building wall and ceiling assembly is reduced, with most being single-layer construction systems. The load-bearing structure itself provides the thermal insulation properties. No additional insulation is necessary, as thermal insulation can be achieved through its deep wall thickness. Wall openings have a deep reveal. Window frames can be positioned at the internal face of the opening, reducing direct solar radiation on the window glazing (see Fig. 3). The need for sun-shading devices and additional sun protection is reduced.
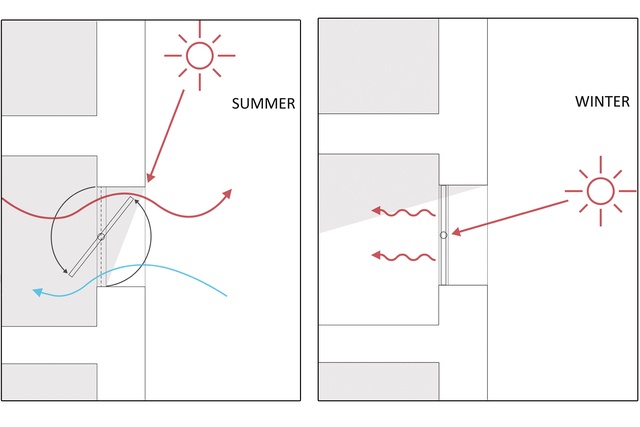
Centrally pivoted, opening window sashes provide effective cross-ventilation. Even a room with only one ventilating wall (single-sided ventilation) can achieve the requisite ventilation by using multiple centrally pivoted window sashes. The use of broad-leafed, deciduous tree planting can assist this; in winter, the façade collects solar radiation and, in summer, the trees shade the façade and reduce solar heat gain. The materials used offer better recycling opportunities; i.e., the brick and concrete buildings avoid any steel reinforcement. That is why the architect decided to use arched windows without steel-reinforced lintels. The different positions of the window are evident in the house section (Fig. 4). A comparison between the Build Simply and the conventional window head section detail of the concrete building can be seen opposite, where in the Build Simply one (Fig. 5, on right) has no additional insulation and no sun blind device is necessary.
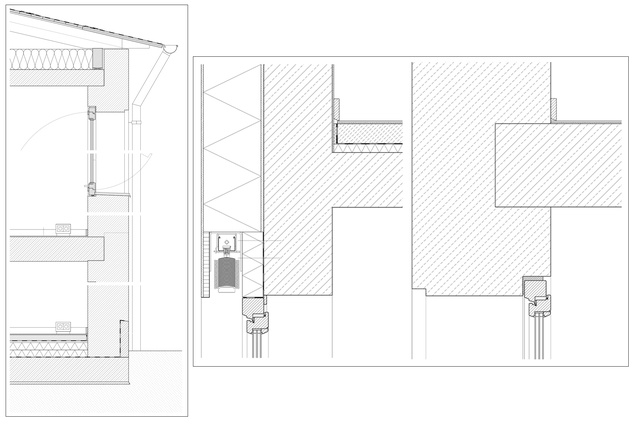
Inside my comfortable pantry in Auckland, I am thinking about the next challenge: How can we best adapt the Build Simply strategy to make it suitable for Auckland, taking the wet, subtropical weather and earthquake requirements into consideration?
Dr Ferdinand Oswald is Senior Lecturer for Architecture Technology at the University of Auckland’s School of Architecture and Planning, a position he has held since 2019. Born in Stuttgart, Germany, he has been granted several European patents and won several research awards, including the European Recycling Award 2015 and the Innovation Prize Architecture and Building at BAU Munich 2017. He is the Principal Investigator of the funded research project ‘Gradient Concrete/Resource- and emission-reduced concrete building construction system’ in cooperation with Prof. Werner Sobek, ILEK, University of Stuttgart.
1 Green Building Award 2011 of the City of Frankfurt, frankfurt.de/themen/klima-und-energie/energie/gebaeude/green-building-award
2 German Urban Development Award 2010, staedtebaupreis.de/wp-content/uploads/2017/
08/07-DSBP-B_FHAM.pdf
3 Award-winner: Recycling Award 2015 – European Quality Association for Recycling e.V. (EQAR), ‘facade4zeroWaste project’, Berlin Rotterdam.
4 F. Oswald, R. Riewe, T. Lueking, K. M. Hengel, W. Wiedenbauer, A. Weier and E. Rauter, Applicant: Sto AG: Method for creating a façade system, 2011, European Patent Agency, EP 2562320 (A1).
5 F. Oswald, Reduce A/C – Reducing the utilisation of air conditioning in high-rise buildings in subtropical and tropical climate regions. Austria: Graz University of Technology, 2016. ISBN 978-3-85125-430-3.
6 Werner Sobek, en.wikipedia.org/wiki/Werner_Sobek
7 Werner Sobek, Valentin Brenner and Petra Michaely (editor Christian Schittich), ‘Buildings as resource stores: Recycling-friendly construction in practice’, Detail Green magazine, 01/2012, Munich, Germany. ISSN 1868-3843.
8 Bauwelt magazine, April 2021, Bauverlag BV GmbH, Berlin, Germany.