The limitless possibilities of robotic fabrication
Lauren Vasey’s work at a digital fabrication unit in Stuttgart researches the combined potential of architecture and robotics. She was here in New Zealand recently and spoke with Guy Marriage, joined by Kevin Sweet, both from the Advanced Manufacturing and Prototyping for Design research lab at Victoria University of Wellington.
Vasey’s work is at the junction of architecture and robotics, an area rich with possibilities for the future. She started off at Taubman College, University of Michigan, USA, doing engineering and sprang to the attention of the Paradigm Shift crew at an Autodesk University conference, examining the human/robotic interface inherent in the Apple Watch.
Now, she is running her own master’s programme on robotic methods and the rich tradition of material manipulation, and her PhD work concerns the new technologies and new possibilities for fabrication in architecture. Together, Taubman College, ETH Zurich University in Switzerland and the Institute for Computational Design and Construction (ICD) in Stuttgart are leading the world in this area; Wellington’s AMPD (Advanced Manufacturing and Prototyping for Design) research lab plans to follow close behind.
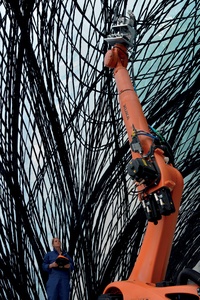
It’s interesting talking to someone as deeply versed in robotic fabrication as is Vasey. Working at Stuttgart ICD, she’s up there with the top researchers in the world in this fascinating, fast-moving industry. Her boss (Professor Achim Menges) is leading the pack and is evidently excellent at securing the considerable amounts of funding needed.
In historical terms, Vasey notes that the use of robots in construction is now well past the stage of ‘merely achieving’ the required levels of precision and, with the integration of sensory feedback into the robots, we are now entering a truly cyber-physical fabrication realm. By that, she means robotics with both computational and physical properties, working together on collaborative goals; in plain English, robots building things together.
To some people, the prospect of robots building things is a terrifying prospect, with visions of job losses interconnected with visions of the Terminator. Relax – it won’t be like that. The point of robotic construction is not to train a mind-numbingly expensive piece of equipment to behave like a chippie with a hammer, nor to create a brickie that can lay bricks non-stop day and night. Truly, the point of robotic fabrication is to do things that have never been done before: to build structures that could exist only in our imaginations until now.
There are numerous projects that have come out of the door of the ICD over the last decade but the one that has the most bravura, chutzpa and sheer amount of inspiration to me is the collaboration her team devised in a large empty room: between two chunky, industrialised robots, a small flying drone and a large spool of carbon fibre filament.
The video shows the seemingly effortless operation; one robot weaves the filament around its end of the structure and passes it on to the aerial drone. The drone then races off down to the other end of the structure and passes the spool of carbon over to the other robot, which, in turn, repeats the motion and sends the drone back again.
Over time, the team of three machines literally weave together a structure that is more Zaha than Hadid herself could ever have been. Not only the materials but the technology as well are pushing the boundaries of architecture. The possibilities are limitless.
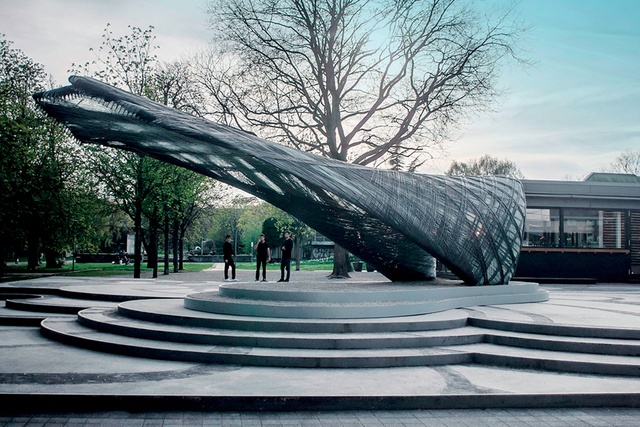
Vasey notes that, although it may look otherwise, it is not completely autonomous – the robots and the drone work via a central web interface, reporting back to the hub, which then releases the next batch of instructions. The spool is held in a magnetic bracket while the robots pass the virtual baton – like a relay race between humans. The whole fabrication process operates as a complete system. Other similar projects involved weaving fibreglass filament over the top of a large inflatable ETFE bubble, building up a structure to form ribs.
The bubble is then deflated and the structure remains. She is busy with another project now, where she is laying chopped strands of fibre and, then, spraying resin over the top but, here, she is not using the drone. Instead, cables run from an overhead gizmo in a manner similar to that of a camera filming sprinters in an Olympic stadium. Her inventiveness is infectious. If it is this much fun, why aren’t we all doing this on site already?
So, what is hindering the construction industry’s uptake of robotics on site or in factories? Vasey suggests that “the construction industry is highly fragmented and, at present, industry just can’t take the risks”.
Kevin Sweet asks her if governments need to step in and take more pivotal roles to redevelop and recognise the current huge need for the world to produce more buildings. “Automation always opens up opportunities for people to be doing something more useful,” says Vasey. “I don’t see a future where robots take over but I do see a future where they contribute significantly.”
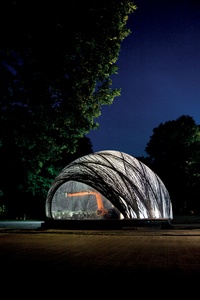
She believes that there is a huge opportunity for more of construction to become automated but she notes that the current industrial robots being used are not really very suitable for the scale and conditions of the modern building site.
Vasey poses the question of who will build the new robots to do the new work. Do we need to redesign the robots to work better for our existing construction systems or do we redesign the way we build to suit the robots better? Do we need to let robots work hand in hand with humans, to collaborate together, or do we envisage a future where robots will work autonomously with little input from humans? How do we want to work with robots in our lives?
I’m very tempted to ask “Who is the boss in the future: them or us?” but I think better of it. I’m also tempted to ask whether or not there is something similar to Isaac Asimov’s famous guiding principles for US robotics – the Three Laws of Robotics – but, of course, I already know the answer is negative.
Asimov’s First Law of Robotics simply and clearly states that “A robot may not injure a human being or, through inaction, allow a human being to come to harm” but the truth is that, so far, humans have been quite poor at programming this into the robotic positronic brains. Our robots do not yet ‘think’ – they are just following orders. We’ve all heard that line before.
“The work you are doing does seem to be very sci-fi, for want of a better term,” suggests Sweet. “On the scale of exploratory research and practicality, at which end do you sit?”
“In the context of a studio, then, this work is super-speculative,” replies Vasey. “However, once the explorations have become more robust, then they become more mainstream.” As an example, Vasey explains her team’s work to create a timber research pavilion to be built in a bundesgartenschau (biennial regional garden show) in Heilbronn in 2019.
So, already, the avant-garde world of the university is entering the mainstream world of the garden show. I ask her if this is having a flow-on effect – is the new building technology being taught earlier in architectural careers now?
Originally, this work was all part of the ordinary architecture master’s programme, taking in ordinary M.Arch students – but now it has its own special degree. Vasey is teaching in the programme, educating about 30 master’s students a year (60 in total for the two-year degree) and, also, is part of the team of around 15 PhD students. In case you’re interested, the programming languages are the same stock-standard languages that we code in here in New Zealand – Rhino, Grasshopper, with Python and C Sharp. But you will need to be special to get in.
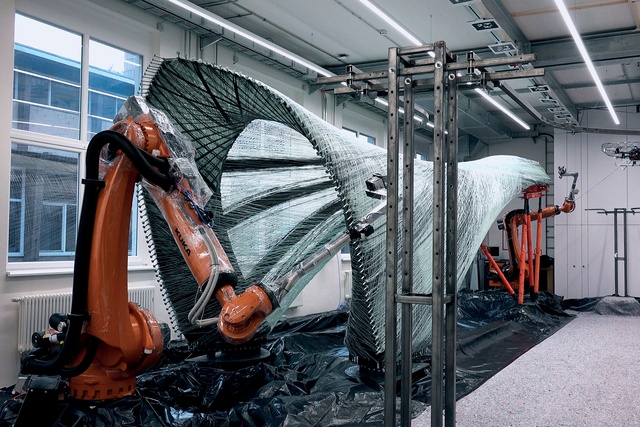
“There is a new field, growing somewhere in between architecture and computational robotics,” says Vasey. “We’re no longer taking general, run-of-the-mill architecture students but, instead, we already require students with a pronounced predisposition towards the computer coding of robots. We have teams of interdisciplinary experts, i.e., students from computational calculation, working with architects, engineers and building science students, all together in a team.”
So, despite the advent of robots, there will still be jobs for architects it seems but, perhaps, not the jobs we do at present – and not the solo starring role of ‘the architect’. The role of the architect will become obsolete as the technology evolves, unless we adapt and change. The role of the architect will certainly be challenged in the future; if we’re not engaged in the discussion, we will become a redundant profession.
But, here, New Zealand is lucky. This is the country to do it in – we’re small, we’re nimble, and we can fail fast, innovate and get back up again. Hopefully, hand in hand with our robot overlords.