Try before you buy
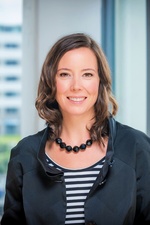
It’s a Friday night after a busy work week – you board the light-rail from Britomart to Hamilton North station and travel 30 minutes taking in a light meal and glass of wine. The train arrives at the HIVE Home Innovation Village where most passengers disembark with their wheelie bags for the weekend stay ahead. A small village of forty state-of-the art demonstration houses await your discovery.
You have already chosen your two favourites, one to stay in tonight and one for tomorrow night. This evening you will stay in a Homestar 9 star-rated house, a cutting-edge ultra-sustainable home achieving zero net energy (think annual electricity bills around $0). Tomorrow you will stay in a similar home built to Lifemark Gold standard, so that you know your investment will cater to your lifetime design needs as you age, alongside being a place where you can host your children and their children.
All of the houses have been built using the latest innovative technology like the homes you see built on Grand Designs – large Lego-like room chunks or stacked panels for walls and floors assembled into a home over a few days. On Sunday you will see one of these houses finish its assembly – it’s all part of the weekend’s activities.
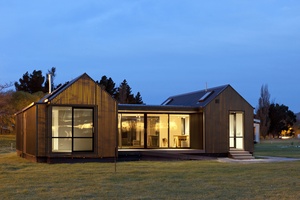
HIVE is the place to go to choose a home, see different houses evaluated side by side, watch earthquake-resistant simulations, see self-cleaning materials at work and all the latest technology. You will get to ‘try before you buy’ and know that your consumer dollar is well-spent because you have seen the innovation, research and development all on transparent display.
You are an empowered consumer. This is the future.
Now come crashing back to 2016 and the way things are today. Most of the house buying and building industry runs on ‘word of mouth’. Most clients change their mind repeatedly during the construction process, resulting in overruns of time and money. The ‘putting it right’ period to fix up subcontractor mistakes can drag on for months and erode any leftover goodwill that consumers have with the construction industry. This is the norm.
But the way it could be is for New Zealand to offer a permanent housing village where consumers have full disclosure of what they are getting, before committing to purchase. It builds on the Kiwi tradition of visiting an isolated showhome and creates a village-scale experience where evaluation of housing options can take place in full view side by side. This happens in Germany and Japan and is highly successful in those cultures where consumers demand access to impartial knowledge.
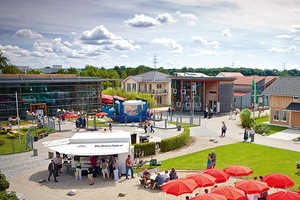
In Germany, there are housing villages with up to sixty homes on display. At Bauzentrum Poing, outside of Munich, an infamous HufHaus showhome (think ‘that’ Grand Designs UK episode) sits alongside more prosaic housing models. Most are standalone two-storey models with walls a foot thick, filled with insulation to protect occupants from the harsh weather conditions. All are delivered in panels to site – a method used for fifteen per cent of German homes today. House manufacture incorporates the latest Building Information Modelling (BIM) types of modelling software that speak directly to machinery on the factory floor. This is an exact process with a defined result.
German customers are notoriously demanding from a sustainability perspective – some even requiring de-magnetised iron beams as supplied by upmarket Baufritz. The housing manufacturers have their own in-house architects and engineers, many have customer-facing demonstration suites at their factories (think beautifully designed Ikea-like rooms), and all have play areas to entertain children while their parents make the largest financial decision of their lives. These housing businesses understand that women are their core customers and the key decision-maker in the home purchase process. They cater accordingly.
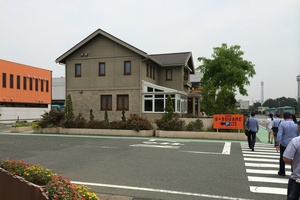
In Japan, the customer experience shifts to the functional aspect of the home. Consumers visit ‘R&D’ facilities at the front of the manufacturing process where they choose fixtures and fittings alongside structural components like seismic-resistant foundation systems. It is a hands-on, interactive experience, with different glazing systems demonstrated using heat-lamps and insulation systems demonstrated using giant walk-in freezers.
By the end you truly ‘know’ what type of performance you want, before signing up to the associated costs. Wall claddings are bombarded with battering rams and fire treatment and you can even experience a simulated earthquake to compare foundation systems with traditional construction. It is alarming and effective.
Japan is the home of an established and sophisticated lean manufacturing industry with housing factories populated by robots, large chunks on assembly lines, and assembling processes akin to vehicle manufacture. Toyota Homes, Sekisui House and Heim, Misawa Homes, Daiwa House and others supply fifteen per cent of all housing in Japan through panels and pods. Sekisui House produces 15,000 detached houses a year, with the factory plant in Shizuoka producing around 20 houses per day. One factory can produce as many houses as New Zealand builds in one year.
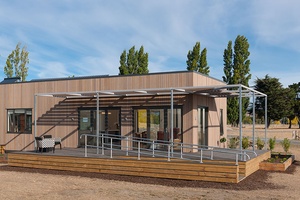
New Zealand industry can learn from Germany and Japan’s client-focused design, consumer experience, and image improvement of prefabricated houses through marketing their quality and range. The emphasis is on both quality and customisation.
New Zealand consumers could have full transparency of housing choices – and get exactly what they thought they were paying for – known quality, known timeframe, known cost, known sustainability features and known architectural design. Prefabrication is the tool to deliver these ‘knowns’ – components, panels, volumes and complete buildings brought to site in prebuilt pieces and parts.
PrefabNZ, the hub for prebuilt construction in New Zealand, delivered the country’s first HIVE Home Innovation Village in Christchurch in response to the Canterbury earthquakes (2010-2012). The village showcased up to ten homes over a two and a half year period. It was supported by housing teams eager to change perceptions about prefab, industry partners such as Meridian, and Christchurch City Council.
The next step is to gather industry support for a permanent HIVE in close proximity to Auckland – this is an invitation to you to join us and board the next train to HIVE.
Contact PrefabNZ at info@prefabnz.com.