In Focus: Building smarter (part one)
We look at what building smarter means for New Zealand and two efficient construction methods as better ways to build in the future.
Innovation is at the core of Kiwi culture and, with increased demand and changes in the way we are living in our houses, it is inevitable that the ways is which we build our homes will change. And maybe those changes are needed. It is estimated that we are building only half of the homes we need and, with well-known issues regarding the quality of our homes and built communities, this is a major social concern. The way we build is more often than not disjointed, inefficient and old-fashioned. Now, more than ever, we need to build smarter.
But what is ‘smarter’? Adopting more digitally led construction techniques and technologies, and ensuring that we consider the whole life of our home – aiming for longevity and quality – are two key moves towards this.
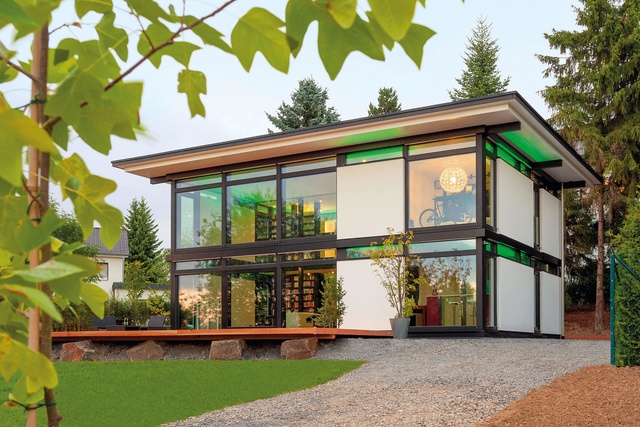
Firstly, building smarter can mean building more quickly and efficiently, and offsite manufacturing is where speed and quality can come together. Throughout history, buildings have been built in one place and then reassembled in another. It is still early days in New Zealand for assembled architecture but some early adopters are showing it can be done in
order to build smarter.
Prefabrication, where sections of a built structure are built off site (usually in a factory) and then assembled (hopefully swiftly) on site, aims to improve productivity and decrease construction costs through reduced labour costs and economies of scale. Modularisation is where whole parts of a built structure are built off site, often without the same level of standardisation. Offsite manufacturing reduces the time and cost of constructing a home and can ensure consistent standards are applied to the home, therefore meeting future demand for quality housing.
Prefabricated: Backyard
There are local examples of a recent uptake in offsite manufacturing and, while some are sceptical about the ability for this to solve our housing crisis, there are clearly some benefits associated with this form of building. At one end of the spectrum, Bunnings Warehouse has introduced flat-pack housing: two-to-three bedroomed, two-bathroomed homes of 40–100m2, selling for $70,000 to $100,000. Steady sales since these packages were launched last year indicate they have met a need in the market.
A more design-focused example of prefabrication comes from the SNUG design competition initiated by offsite manufacturing advocacy group PrefabNZ. The competition asked designers and architects to design a complementary backyard dwelling. It required the entry to be no more than 65m2 to meet the definition of a minor dwelling, which, as per Auckland Council’s regulations, is a small, stand-alone unit that is on the same site as an existing standard household.
The benefit is that, often, a minor dwelling can be built on a site where an additional full household unit cannot be built. Entries were required to be able to be made off site and transported to site for assembly. With the idea that a buyer could pick their house type from a catalogue, the competition was very successful.
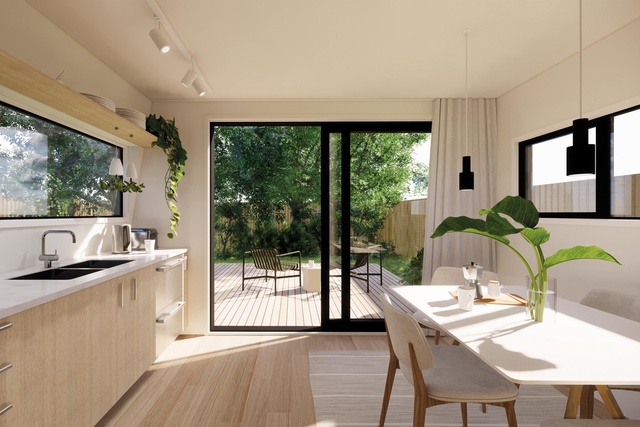
The Flip, designed by architectural practice First Light Studio, won the People’s Choice Award. With the option to be panellised, it can be either one or two storeys, depending on whether the home is ‘flipped’ up or laid down flat. This unique concept has gained traction, with more than 200 enquiries generated so far, prompting the architects to design a range of different houses, of between 42m2 and 81m2.
“The biggest thing holding back building in New Zealand is the availability of land,” says Flip designer Eli Nuttall, “but people are starting to see their backyards differently and to realise the potential opportunities that are available on land they already own.”
The Flip’s small footprint is both physical and environmental, with its walls 50 per cent thicker than is prescribed by the standard building code, allowing for added insulation, and its thermally broken, double-glazed windows and flexible orientation making the most of the sun and warmth year-round. It also offers optional photovoltaic solar energy, rainwater collection and grey-water recycling.
The Pitch by Sheppard & Rout Architects and Portabuild is another thoughtfully conceived design, with its re-imagined monopitch roof creating a unique silhouette and interest from every angle. Architects Jonathan Kennedy and Duncan Barron have worked in partnership with Portabuild to reconfigure an existing panel-based construction system to deliver a contemporary architectural solution.
Within the assembly line, exterior cladding options, floor-plan configurations and internal joinery finishes can all be individually selected, making for a highly versatile structure.
“The Pitch layout has been designed so that secondary modules can be added to the main form at a later date, with little change to the original structure,” explains Kennedy. “This should work well for larger or extended family groups.”
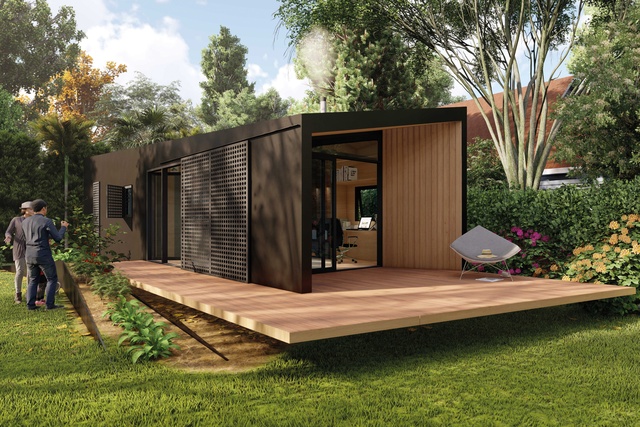
South American architecture studio MAPA began developing its prefabricated Minimod range in 2009, completing the first prototype in Brazil in 2013. MAPA says that the original concept was to offer compact, efficient designs “that enhance their surroundings and turn them into available landscapes”. With an emphasis on quality design, the Minimod is being marketed here in New Zealand by Makers Fabrication as a high-end retreat for remote, natural locations.
Based on what the studio describes as “prefab plug-and-play logic”, cross-laminated timber (CLT) provides the building framework – featuring on the floors, walls and ceiling – but buyers can choose from a number of exterior claddings, including black-charred timber, polished metal and cement boards.
Prefabricated: Stand-alone
In TOA Architects’ Tuarangi House in Grey Lynn, the walls, floors and roof are all made up of 43 prefabricated CLT panels. This move enabled the structure of the 156m2 house to go up in just 10 days with greatly reduced construction waste. Designer Craig Wilson, a member of PrefabNZ since 2015, says he and the team at TOA have really tried to push the envelope with what they can do with CLT and are looking to test innovations within the construction industry to make things simpler and faster.
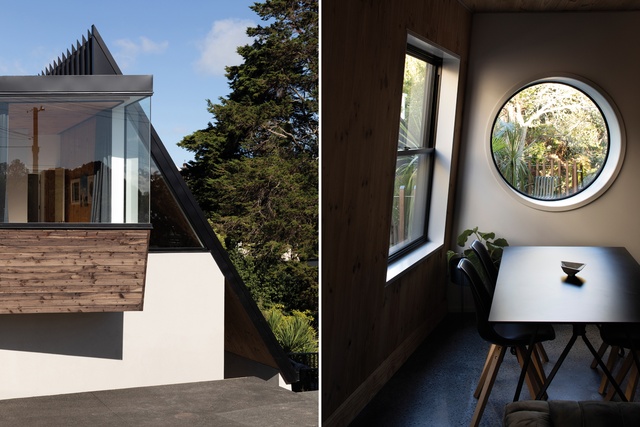
The panels were manufactured in Nelson by XLam, travelled to Auckland in two truckloads and were assembled on site by the builders with the help of the crane drivers. “The greatest saving this achieves is in time,” says Wilson. “With two of the biggest increases in building costs recently being labour and kit (e.g. scaffolding), there’s a definite saving there but it’s more complex than that. The cantilevered southern wing is formed as a single structural element, similar to a giant box beam made from CLT panels – this allows the structural element to be inhabited and, with the exposed timber interior, exposes the honest materiality of the CLT.”
Architectural practice Tennent Brown responded to the challenges and cost of building in a remote part of the Marlborough Sounds with the design of its 2019 NZIA Local Award-winning Te Ngāhere Hou.
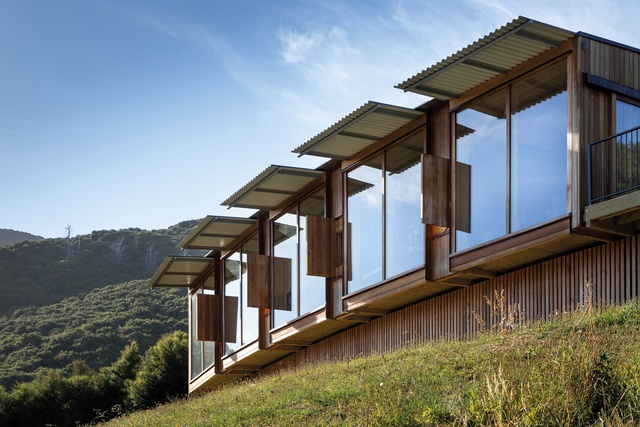
The largest ‘truckable’ modular elements (3.2m x 6.3m)were built in the local builder’s yard and joinery shop, 1.5km from the site. The elements, with glulam portals each side, were then arrayed on site in a gentle arc, formed by interstitial spaces for shutters, thermal mass floors and flashed joints to roof and rear walls.
Architect Hugh Tennent says that while prefabrication requires industry capability and greater design time, “it delivers a superior design outcome, with fast, efficient and high quality construction.”
In Australia, John Wardle Architects is in the process of building the Limestone House in Melbourne’s Toorak to Passivhaus and Living Building specifications. Architect Diego Bekinschtein says their client had previously built a prefabricated house in Italy and it tied in well with the project’s environmental initiatives. “The benefits dovetailed together because a Passivhaus home requires a lot of taped seals and tight building tolerances, which are far easier to achieve in a clean factory than on a dusty site,” explains Bekinschtein.
The prefabrication process, in partnership with prefab architecture firm ARKit, was not the typical one of modularisation. Here, each panel was a different shape and form, “but we still benefited from quality control, waste management, time management (thanks to wet and heat on site) and working with tight site constraints,” says Bekinschtein. In addition, the basement structure could be progressed by head contractor Sinjen while the panels were being fabricated in the factory.
Read two more methods of smarter construction in part two of the Building Smarter feature.
This article first appeared in Houses magazine.
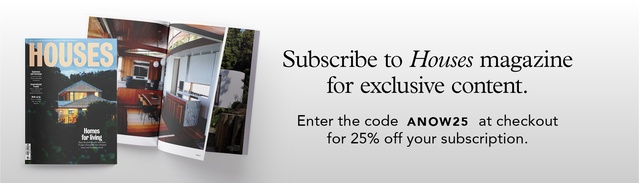