Allproof’s new solar panel install saves 50 tonnes of C02 every year
Partner content: The process is just as important as the product. This underscoring principle has driven Allproof’s local manufacturing focus in recent years.
As a manufacturer of market-leading plumbing and drainage products, Allproof understands its environmental responsibility and takes it seriously. Allproof is striving to be an environmentally conscious manufacturer while continuing to produce premium products for the plumbing industry. Allproof firmly believes that the production process is just as important as the quality of the products that it produces. This has led to a targeted investment in its North Shore manufacturing facility, which includes new, energy-efficient injection moulding machines and clean, renewable solar energy to power them.
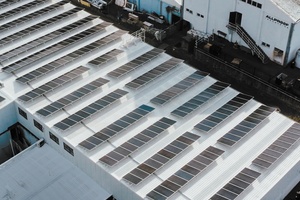
Allproof has recently completed the installation of 449 solar panels through solar installation company, Solarcraft. The installation took six months of initial planning, followed by a team of five working for 900 hours over a four-and-a-half-week period. This marks a key milestone for the company and underscores Allproof’s desire to be an industry leading manufacturer with an environmental conscience.
The projected daily average of 750kWh of clean, renewable energy (in excess of 1,000kWh per day during summer months) generated from the 1700m2 solar panel installation is used to power Allproof’s North Shore head office. The building houses its injection moulding, product assembly and outward goods departments. This will provide Allproof’s main facility with nearly 50 per cent of its energy needs sourced from self-generated, clean solar energy. To give context, this is enough power to supply approximately 34 average New Zealand homes per year (www.ea.govt.nz/consumers/what-is-electricity). Excess power generated through peak production times is supplied back into the grid for local homes and businesses to benefit from clean energy. This impressive solar panel installation saves 50 tonnes of CO2 from entering the atmosphere every year.
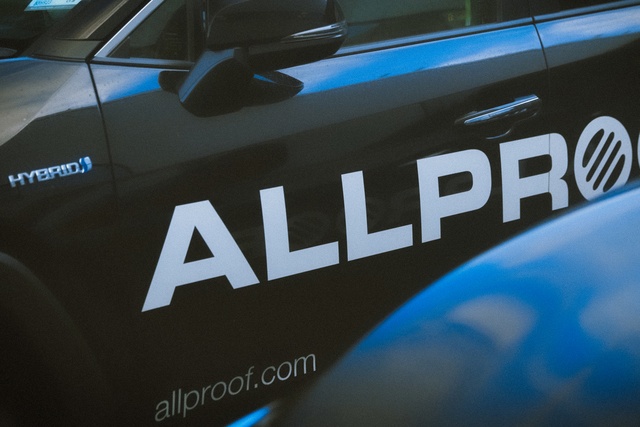
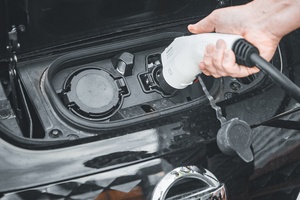
Another benefit to the onsite production of clean energy is the ability to charge Allproof’s plug-in electric vehicles (EVs). By charging the EVs onsite, Allproof can utilise the clean, renewable energy it generates to significantly reduce the emissions of vehicle kilometres driven. Accompanying the plug-in EVs, Allproof is also upgrading its fleet of sales vehicles to hybrid electric vehicles. These vehicles have improved fuel efficiency, reducing CO2 emissions while allowing the sales team to continue to offer the high level of service required by customers nationwide.
In addition to these developments at Allproof’s manufacturing hub, the company continues to increase its range of drainage and passive fire protection products made from 100 per cent recycled plastic. Through their use of recycled plastic for the production of these products, Allproof prevents over 12 tonnes of plastic from going to landfill every month — that’s the equivalent of more than 152,000 two-litre ice cream containers per month.
These recycled materials are locally sourced from kerbside collections and allow Allproof to provide a large range of secondary recycled products, enhancing the lifecycle of these plastics, produced with a focus on sustainability and an overall reduction in environmental impact. Furthermore, Allproof also holds the Best Environmental Practice (BEP) Certification for the production of PVC products, as part of its wider AS/ NZS1260 product certification.
For more information, visit allproof.com or call 09 481 8020.
This content has been created with support from Allproof.
ArchitectureNow works with a range of partners in the A&D supply sector to create and/or source appropriate content for this website and Architecture NZ magazine.
If your brand or clients are interested in similar creative content email mark.lipman@agm.co.nz to enquire.