The final push: SGA and A+W•NZ Motu Kaikoura workshop
Maria Hosking from SGA reports on the installation and finishing of the SGA and Architecture+Women•NZ Motu Kaikoura Building Workshop.
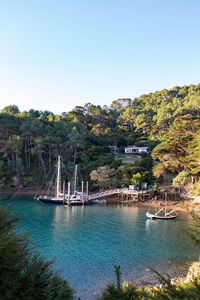
The kitchen/dining/living facility for the Motu Kaikoura Community Trust is almost complete, and what a life-changing process it has been. The 20-week course, led by Strachan Group Architects’ director Dave Strachan, invited 16 practicing architects and architectural graduates to prefabricate the SGA design in the SGA Workshop in Kingsland for final transport to Kaikoura Island (off Great Barrier Island) in the Hauraki Gulf.
The first weekend of December 2017 was set for the dismantled and rigorously packaged building components to be transported by road, sea and sky to the remote and protected island. We had successfully completed other prefab projects transported by Hiab truck in various modular and/or panelised states, but this was a whole new ball game.
The logistical nightmare of orchestrating the various transport methods and companies, biosecurity checks, tools, materials, fixings and finishes (it’s a long way to go if you are short a screw!), plus food and supplies for the 16 volunteers, four builders, Dave and myself, was challenging to say the least… and of course it would be up to mother nature to make the final call.
Our prayers for good weather were answered and on 30 November 2017 we travelled by chartered boat to the beautiful Kaikoura Island. Tensions were high after a grave Health and Safety induction with Hamish, our pilot from Skyworks – this was to be an intense and possibly dangerous three days of action and we all had a part to play to ensure that it ran smoothly and that no-one’s safety was at risk.
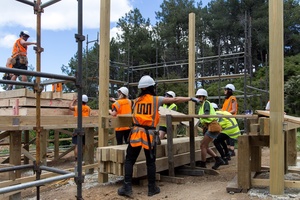
We arrived, set up camp and got to work straight away preparing the building site, checking the foundations and subfloor installed by local builders, marking heli-drop points, running through the order of events with the team and talking through the many diagrams and spreadsheets that we had prepared to ensure things were clearly communicated and ran to plan. A safe zone was marked out, code words and various roles agreed on. We were ready…
Day 1 – Floors
The floor cartridges (prefinished plywood, LVL framing, insulation and underply) had been packaged in stacks of two to three and coded for transport and assembly. The four builders from Crate Innovation and JR Hosking Carpenters & Co. balanced on the bearers and scaled the scaffolding to receive the 600–900kg packages that came in thick and fast in 6-minute intervals. Pressure was high and in just one hour, the floor cartridges were all in place, screwed together and ready for fixing to the subfloor.
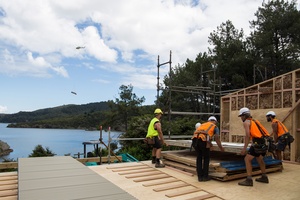
All 17 of us girls ran excitedly under the subfloor to apply the many ‘z’ nails and nail on plates – the sound of that many hammers going at once was deafening but exhilarating! That evening we had a drink on the complete floor and admired the elevation and view. Day 1 was a success – tomorrow we would receive and stand the walls.
Day 2 – Walls
It was Saturday morning and we were in for another beautiful calm and sunny day. Dave was brought over by the heli crew after overseeing the transport of the remainder of the building from SGA Workshop to Wynard Quarter the evening before. We saw the chartered vessel arrive in the sheltered passage out from the site that was formed between Kaikoura Island and Great Barrier Island.
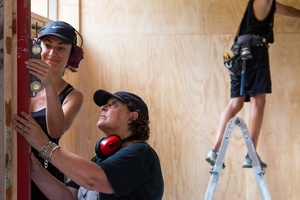
A couple of us shot across by speed boat to check the 17 packages and run through the plan with the Skyworks ground crew on the barge deck. After sorting a couple of hiccups, we were ready to begin. The completed floor platform made it safer to receive the flat-packed prefabricated wall panels (LVL framing, insulation, RAB, Metalcraft corrugate cladding with windows and glazing installed(!)), however we would need to unwrap, stand and fix wall panels between drops, which we knew from the day before unfolded very quickly.
Intermediate drops of interior linings, cabinetry, roof panels, decking etc. were dropped off in specific locations around the site to buy us time standing panels. Pressure was high and when the last wind beam piece was lifted into place by helicopter we all cheered with relief and satisfaction – we had pulled it off! We had done what some thought was impossible for our unique team.
Day 3 – Roof
While the builders manhandled the 70kg Thermospan SIP (Structurally Insulated Panel) roof panels on to the site, the rest of us carried on with fixings, sealants, undercladding, laying decking, sorting materials and installing the overwall cedar sliders.
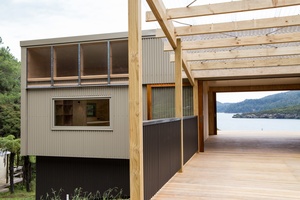
By that evening we had the roof on and boy did we celebrate, with more delicious cooking from the tightly rostered meal plan, whisky and Dave on the guitar.
The building was left weather tight and locked up over the summer break. Following the pre-line inspection, those from the team that could make it (plus our plumber Tim of Flux Limited and electrician Lloyd of R.C. Gregory) returned to complete the interior lining, cabinetry, services, decks and pergola. The week was, once again, not for the faint hearted! But the weather was great, the sea refreshing and the company outstanding.
The whole project has been invaluable beyond measure for all of us and we often discuss how it’s hard to communicate to others just how significant the experience has been. Although incredibly challenging in more ways than one, we all feel very proud of each other and of the building that now nestles into the landscape as though it were always there. The friendships made and skills gained will be ones that will last a lifetime.
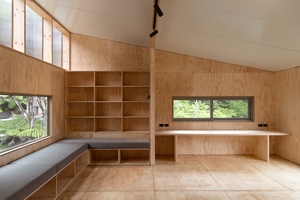
The project could not have been possible if it weren’t for the sixteen women who gave up their Fridays and weekends for weeks on end to learn new skills and become better architects. Their generosity and dedication has been unstoppable, and their families, employers and clients that have supported them through this process must be thanked too.
To the many sponsors of building materials and course fees, we thank you for your support and for making this exciting project plausible. We hope that the experiences the new building offers will encourage others who have a passion for New Zealand’s natural heritage to visit Motu Kaikoura and become active participants in its restoration.
You can read the first blog post about the workshop here, and the second here.
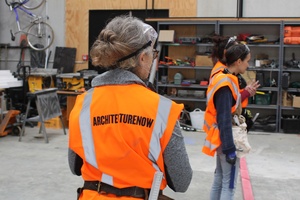
The valued sponsors of the SGA and A+W•NZ Motu Kaikoura Building Workshop were: APL, ArchitectureNow, Blum, Bunnings, Carter Holt Harvey, Cutshop, Fires by Design, Franklins, Fortress Fasteners, GIB, Katalog, LightPlan, Metalcraft, Metro Glass, Nicks Joinery, NZ Steel, Plytech, Prime Panels, Proclima, PSP, Resene, Rinnai, Rosenfield Kidson, Sika and Spax.
ArchitectureNow sponsored Pip Newman, a tutor at Unitec, and would like to congratulate her personally and the rest of the team for the incredible job they’ve done with the Motu Kaikoura project.