In Focus: Building smarter (part two)
In part one of this In Focus special, we discussed what “building smarter” means for New Zealand housing, and we looked at two solutions that may lead us to better outcomes for the future: prefabricated backyard dwellings and prefabricated standalone homes. Here, we explore two more alternative methods of construction and have a Q&A with the CEO of PrefabNZ, Scott Fisher.
Prefabricated: Multi Unit
When driving into Auckland’s Hobsonville Point, it doesn’t take long to spot the striking development which illustrates the benefits of offsite manufacturing or assembled architecture on a larger scale. The Grounds is made up of 42 one-and-two-bedroomed apartments over three storeys and is built of prefabricated, engineered tall timber – a low-energy material which claims to cause less wastage and pollution than do other comparable materials. The innovative design, developed by Peddle Thorp, includes various engineered wood products as its primary structure; those products are all fabricated off site.
The Grounds is an example of smart building, through both its partial offsite manufacturing but also its carefully considered design, which offers built-in value and quality, including north-facing balconies off each unit. Using offsite manufacturing to create homes at scale, which have a certain level of affordability but are elegant and clever as well, is building smarter. More of these are being rolled out elsewhere in Auckland and many design practices are also experimenting with assembled architecture. It is clear that medium-density projects are where the benefits of this smart way of building are going to be seen most often.
High-Performing Homes
Building smarter can also mean building healthy, warm, dry, secure and insulated homes and urban environments. Ample sunlight, good air quality and low air moisture should all be standard practice. Not only should our homes nurture and protect us but these homes should be part of a built community environment that does the same.
In the future, it would be beneficial if more New Zealanders chose to build beyond the building code and incorporate sustainable and high-performing design and features into their homes. Various movements are changing the way we think about high-performing houses, such as the Passive House Institute New Zealand and Zero Energy House, and a number of developers and builders are choosing to build to higher Homestar standards run by the New Zealand Green Building Council, a not-for-profit organisation working to make all homes in Aotearoa healthy,
warm and dry.
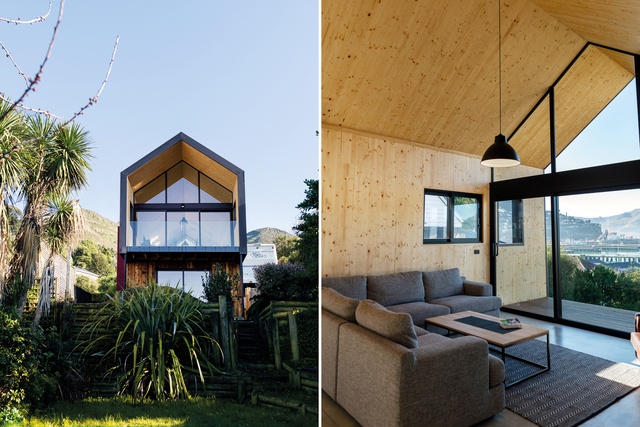
Given the fact that, on some days, we spend the majority of our time in our homes, good indoor environment quality (along with thermal comfort, using low-toxicity products and materials, etc.) is crucial for the overall wellness of the population and, therefore, an important area on which to focus. Building healthier, more-efficient, high-performing and long-lasting houses is smart.
Boat Shed House in Lyttelton, by French architect and eco-advisor Julie Villard, incorporates a number of features that maximise energy efficiency. The result is that the 127m2 project achieved a 9 Homestar built rating from the New Zealand Green Building Council (out of a possible 10).
The 2019 Architectural Design Award-winning house follows the European building code for insulation and air-tightness, using untreated CLT panels from a renewable source and effectively ‘storing’ close to 460 tonnes of CO2. “We were also the first house in New Zealand to use an eco-friendly 100mm semi-rigid wood-fibre insulation that I used back in Switzerland,” says Villard. “Basically, you wrap your building in it, screwing it to the outside of the CLT and then covering it with a weather-tight membrane.”
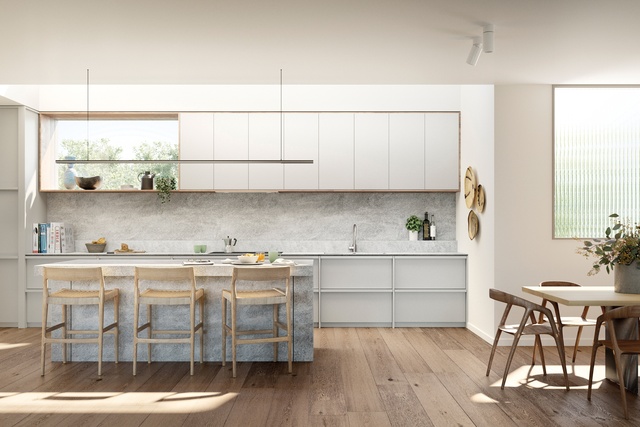
Separate heating, hot-water and ventilation systems are all managed by WiFi on Villard’s phone, along with her lighting and alarm, through Schneider Electric’s Nero app. “Homestar requires you to be efficient with every single item and, if the systems work together, you will reach another level of efficiency,” she explains. “Roughly 50 per cent of your Homestar points are related to the performance of the building and the other 50 per cent are related to you, the user. So, having a usable productive garden is important, as are how you manage rainwater and waste, and how much natural lighting you have – Homestar is basically a way of life.”
In Australia, Hip V. Hype has collaborated with architectural practice Fieldwork to design Ruskin Elwood – four environmentally responsible homes which will be run almost entirely off renewable power with onsite solar panels, electric heat pumps for hot water, hydronic heating and Tesla Powerwall batteries, ensuring uninterrupted energy supply and significantly reduced energy costs.
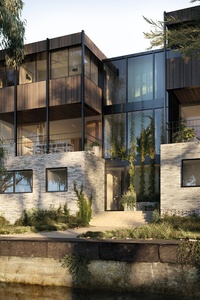
“This project sets a new standard in premium, low-impact living,” says Hip V. Hype founder Liam Wallis. “Our sustainability team has ensured that each residence will achieve exceptional environmental performance and ease of use, with a 7-star minimum NatHERS rating target set for the project.”
Due for completion later this year, Ruskin Elwood follows on from the studio’s recent collaboration with Six Degrees Architects to create Nightingale 2.0, a low-energy, mixed-use apartment and retail building in Melbourne. Located on just 500m2, this 20-apartment project is 100 per cent electric, with power generated on site thanks in part to solar panels on the roof.
Construction in New Zealand is currently slow and expensive, and our homes are often built with a lack of quality and performance. We need our future homes to be efficiently constructed (without the huge price tag), high performing, environmentally considerate and designed for health, and built to last. It is an exciting challenge for designers, architects, home-owners and all Kiwis.
Q&A: Chief Executive Officer PrefabNZ Scott Fisher
How can offsite manufacturing save a home-owner money?
Scott Fisher (SF): Weather currently causes delays of more than 13 per cent of construction time – saving time is the fastest way to save money. Moving owners into their homes earlier means less money spent on rent and bridging finance, and faster build times also enable more houses to be built per year.
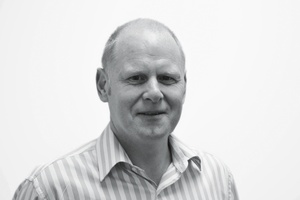
Does offsite manufacturing necessarily lead to better quality?
SF: Past booms show that, when construction demand goes up, quality goes down. Offsite manufacturing provides the consistency of quality that is centred around a better design phase before building starts and robust internal QA procedures within a controlled environment. This means less onsite problem-solving that can lead to sub-standard work.
Are there other benefits associated with offsite manufacturing?
SF: Offsite manufacturing can mean a saving of about 15 per cent in total construction cost. Any savings in construction costs can then be funnelled into increased offerings towards healthier homes. Healthy homes should be a building standard, not an unaffordable luxury. Insulated homes lead to increased productivity through fewer days off work sick, fewer doctor visits and decreased health spending, and lower home energy use with smaller power bills.
It’s important that house buyers recognise the importance of lifetime value in their houses, not simply initial cost. Equally, banks could recognise these benefits and offer the home-owners financial incentives to encourage better design.
Read part one of the In Focus: Building smarter feature here.
This article first appeared in Housed magazine.
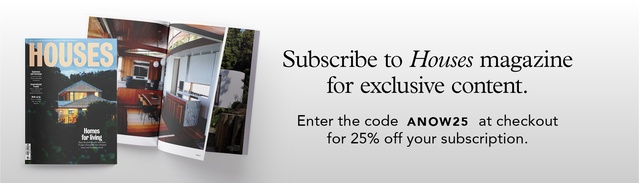